Sandia invents method to integrate microscale optical devices on silicon microchips
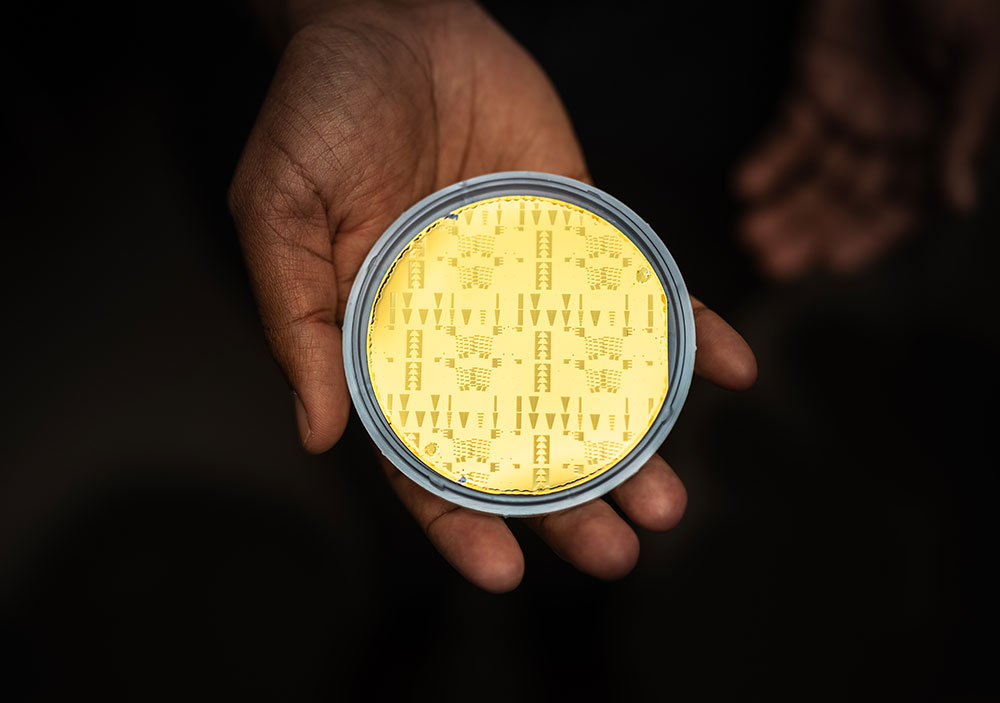
The laser is so small you need a microscope to see it properly. But it’s not just the size that scientists at Sandia are excited about.
The buzz is that the laser can now be combined with other microscale optical devices to make self-driving cars safer, data centers more efficient, biochemical sensors more portable, and radars and other defense technologies more versatile.
Sandia has been awarded a patent for its new method of integrating many different materials onto silicon — the same starting material semiconductor fabrication plants use to make microchips.
This method enables Sandia to build high-bandwidth, high-speed optical devices, including indium phosphide lasers, lithium niobate modulators, germanium detectors and low-loss acousto-optic isolators — all critical components for high-power optical systems.
Building a laser on silicon is a challenging and unusual feat that could extend America’s leadership in semiconductor technology. Other organizations, including the University of California, Santa Barbara, and Intel Corp., have built similar lasers, but Sandia has broadened the class of devices that can be integrated. For the first time, these devices could work together on optical microchips, also called photonic integrated circuits.
“This allows the U.S. to lead and have less dependency on foreign manufacturing capabilities,” Sandia’s Patrick Chu said.
Patrick co-leads the National Security Photonics Center, a group of more than 60 photonics scientists and engineers at Sandia’s Microsystems Engineering, Science and Applications complex.
Integration with silicon a key step toward future production
Silicon is the lifeblood of the semiconductor industry and a great material for making computer chips. However, by itself, it’s a lousy material for making lasers, said Sandia research scientist Ashok Kodigala, a co-inventor of the new integration process.
His challenge was to design a way for optical components made from a variety of materials to coexist on a silicon microchip.
These kinds of materials can’t just be glued into place, so instead Ashok fused them to silicon in complex layers, a process also called heterogeneous integration.
The Sandia team successfully demonstrated heterogenous integration techniques to create hybrid silicon devices: hybrid lasers and amplifiers made from both indium phosphide and silicon, and similarly modulators made of both lithium-niobate and silicon, which encode information in light generated from the lasers.
Moreover, high-power and high-speed germanium detectors were developed to keep up with the lasers and modulators under the same platform.
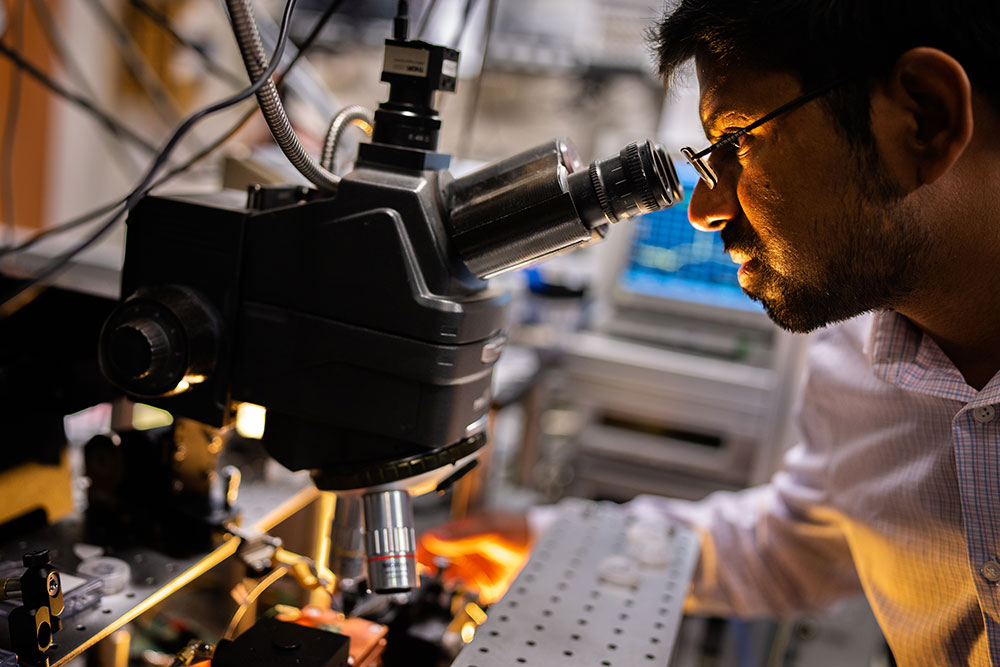
While Ashok and his team are motivated by the progress they’ve made, they say they need to further refine their methods with industry partners before photonic chips can start rolling off the production lines.
In future research, Ashok is hoping to combine lasers with the other optical components onto a single chip.
Semiconductor fabs could use Sandia technique
Sandia built its chip-scale lasers with a goal of transferring the technology to industry. The team used many of the same tools found at commercial semiconductor plants, and the lasers generate light in wavelengths commonly used in the telecommunications industry, called the C-band and the O-band.
“Once we demonstrate this photonic platform at a national lab, we can then pass this technology to U.S. companies, where they can focus on even larger-scale production for commercial and U.S. government applications,” Ashok said.
He conceived his method with funding from Sandia’s Laboratory Directed Research and Development program and developed it under a Defense Advanced Research Projects Agency program called Lasers for Universal Microscale Optical Systems.
Photonic semiconductors support CHIPS and Science Act
President Biden made headlines in 2022 when he signed the CHIPS and Science Act, a nonpartisan, $52.7 billion boost for the semiconductor industry. While the legislation is expected to increase production of American-made computer chips, it also directs funding for photonic semiconductors.
Sandia is also investing in optical microchips because they transmit more information than conventional ones. But manufacturing challenges have prevented their widespread adoption, Patrick said. Even though the technology is well known in scientific circles, on most microchips, he said, electronic technologies still reign supreme.
With a working platform to build photonic circuits, Sandia has positioned itself to support industry and other institutions performing photonics research and development in the coming years. Sandia research is not currently funded by the CHIPS Act.
“We know our process is scalable, so that’s one way we’re supporting the CHIPS Act mission,” Patrick said. “Sandia is eager to collaborate with others and start building new technologies together.”