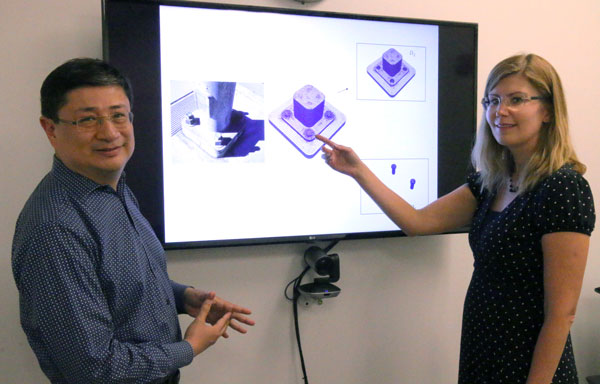
After more than five years, a mathematical breakthrough devised by a structural engineer and a computational scientist may save Sandia time and resources to test complex systems.
The problem with multiple scales
Mechanical engineer Alejandro Mota began working on trying to reduce the time it takes to computer-model systems of numerous large and small components with the same amount of fidelity and detail.
“If you want the smallest components, like the nuts and bolts, and everything else in very high resolution, it would be computationally prohibitive,” Alejandro said. “It would take so long — with the same level of detail in all the small parts — that it would be essentially useless.”
Sandia tests and produces a variety of weapons systems, and the ability to test every component independently and in concert with one another is vital.
“Models are really hard to build when there are different scales involved — that is, when you have an object that has really small pieces together with large pieces,” said computational scientist Irina Tezaur, who started working with Alejandro in 2015. “If you use the smallest scale everywhere to ensure that your simulation is able to resolve everything, you will end up with really a crazy amount of computations.”
Scientists can deal with this by generating a single multiscale model, or computer mesh, of the object of interest. Unfortunately, if the object is complex, this so-called meshing process can take months.
19th century inspiration
Alejandro had tried several methods to make computer modeling better. Then he and Irina began thinking about the Alternating Schwarz method, developed in the late 19th century by German mathematician Hermann Schwarz.
“In 1870, he had this problem with a circular geometry and a rectangular geometry,” Alejandro said. “He knew how to solve both problems separately. But he wondered if he could combine them to obtain a solution for the geometry of both of them combined. He figured out you can.”
Irina said they applied that thinking to calculating models of component parts of a whole system.
“Suppose we have a system where several plates are bolted together,” she said. “Rather than solving the relevant equations on the whole geometry all at once, you solve the equations first for the bolts, then on the plates, incorporating into this second computation the first solution obtained on the bolts.
“You repeat this process many times. The configuration changes during the computation because, at each iteration, information propagates from one region to the other. This links the regions together — couples them.”
Alejandro said the years of research, funded through the physics and engineering models and advanced simulation and computing programs, would not have been possible without the support of their sponsor, Eliot Fang.
“I first started talking to Alejandro about this three years ago,” Eliot, who manages the funding, said. “When you evaluate projects, you are not guaranteed an outcome. This is called R&D risk. But all the surprises in this are on the happy side. Both Alejandro and Irina are highly capable. It was a blast for me to work with them.”
21st century solution
Alejandro and Irina began using the Albany coding test bed and Trilinos suite of algorithms to test their modeling method. The method also works to model the structural integrity of different materials.
“You have these two pieces of metal and a weld connecting them. You are going to stretch it and you want to see how the weld is going to fail or what’s going to happen to it,” Alejandro said, adding that because the method allows elements of a system to be separated, computing resources are needed only for creating the fine details of the immediate area of the weld, rather than modeling the entire system.
“If you have a problem that’s going to take months to compute, we believe we can reduce that to weeks,” Alejandro said. “People want to simplify this problem in order to obtain answers in a reasonable amount of time or with reasonable computational resources. It’s labor intensive and computationally expensive.”
Irina said that the method will really save time when researchers want to model multiple designs.
“If you want to play with different designs — bolts with threading, bolts without threading and so on — for each one you will have a substantial savings,” she said. “You will not have to spend all that time — months, possibly — creating a single model or mesh for each variation. The more designs you want to test, the more savings you’re going to have.”
Eliot said the method has already created demand.
“There are teams with mechanical analysis problems that are actually waiting for this method to be approved so they can apply it,” he said.
A world of possibilities
Alejandro said the method is now being used in production at Sandia in the Sierra code. He and Irina agree that the potential of the method is limited only by the imagination of the researchers.
“There’s some art to it,” Irina said. “For each problem, you have to have some intuition about how to break up the relevant geometry into small and large scales.”
Alejandro agreed that the art is in how you use their method.
“You name it: engineering systems, biological systems. You can go wild imagining where you can apply this,” he said.