At hypersonic speeds, an atmospheric flight vehicle must survive the intense aerodynamic heating environments that are transferred from the hypersonic flowfield to the vehicle surface. The vehicle configuration and external conditions define the heating distribution on the vehicle and the type of thermal protection system necessary to protect its internal components. The Sandia Parallel Aerodynamics and Reentry Code (SPARC) simulates the aerodynamic environment and material thermal response for atmospheric flight vehicles from subsonic to hypersonic speeds—enabling the design, development, and analysis of such vehicles with higher fidelity and more quickly than previously possible.
SPARC solves the compressible Navier-Stokes and Reynolds-Averaged Navier-Stokes (RANS) equations for both laminar and turbulent flow. To do so, SPARC employs several working discretization schemes, with a cell-centered finite volume discretization as the primary scheme. High-Mach number flowfields are achievable through finite rate multi-species reacting gas and two- or three-temperature thermal non-equilibrium models. SPARC’s cell-centered discretization scheme allows for solutions on both structured and unstructured meshes, which enables the simulation of complex and diverse vehicle geometries to meet evolving mission needs.
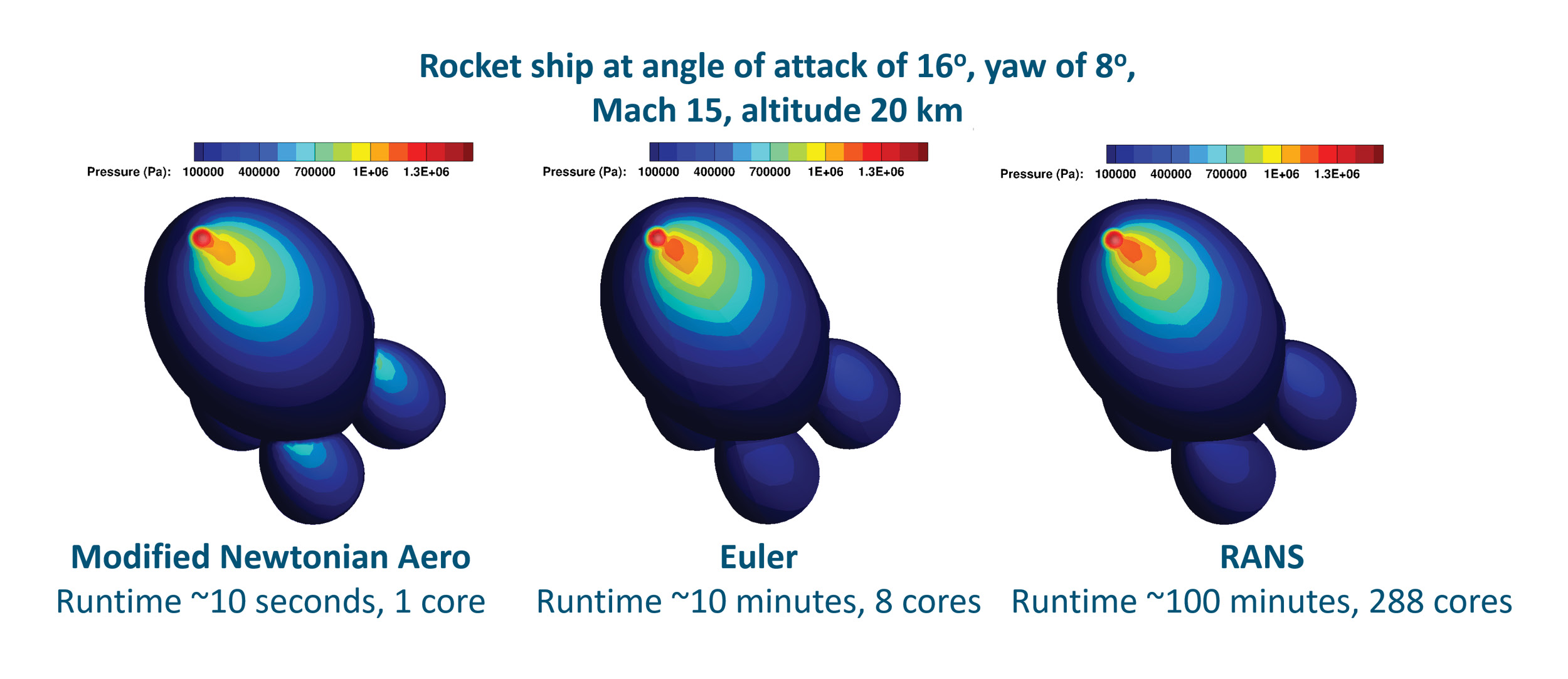
SPARC’s principal applications are in computational fluid dynamics (CFD) analysis of transonic flowfields for gravity bomb analyses and hypersonic flowfields for reentry vehicle analyses. SPARC is also used to simulate the material thermal response and ablation of thermal protection materials (TPS). One-way and two-way multiphysics couplings exist between the CFD and ablation solvers within the code, enabling a coupled “virtual flight test” capability to simulate vehicle response from release to impact.
For reentry applications, a sacrificial thermal protection system (TPS) is often employed, which mitigates the heat load by radiating it back into space, conducting it into the body, or through internal decomposition of the TPS material. SPARC’s ablation module solves the transient heat equation and associated thermal response and ablation equations for both non-decomposing ablators, such as carbon-carbon, and decomposing ablators, such as carbon-phenolic. SPARC’s ablation module can be run for both full 3D problems or more rapidly for 1D problems using a specialized version that incorporates an internal 1D automatic mesh generation capability.
A differentiating capability of SPARC is its Multi-Fidelity Toolkit (MFTK), which employs three different levels of fidelity to produce aerodynamics and aeroheating environments.
These can be tailored to the level of rigor required by a problem. The lowest fidelity is a Modified Newtonian Aerodynamics (MNA) method with boundary layer corrections. Solutions are achievable on complex geometries in just seconds and require very low hands-on subject matter expert (SME) input. This method is suitable for rapid-turnaround design studies employing hundreds of thousands to millions of solutions.
The mid-fidelity is an inviscid SPARC solution coupled with a momentum energy integral technique (MEIT) boundary layer correction. Solutions are achievable on complex geometries in just minutes, but unlike the MNA method, significant SME input is required to generate a computational mesh for the Euler solution. However, by decoupling the inviscid solution from the viscous terms, this approach avoids the gridding requirements of the viscous boundary layer in the non-linear solver, thereby reducing both cost and fidelity. This method is suitable for medium-turnaround engineering-fidelity analyses employing hundreds to thousands of solutions.
The new capability will modernize/parallelize/automate the simulation process and generate a common interface for each of the software tools.
At the highest fidelity is the full RANS capability of SPARC, which models the majority of flow physics observed in real flight. Effects such as shock-boundary layer interaction, separated flow, and fin-fin interactions (critical for maneuvering systems) are naturally captured in RANS solvers. Solutions are achievable on complex geometries in hours. This fidelity comes with the highest computational cost and the highest burden of SME time to generate a computational mesh and slows down the time to solution considerably. This method is suitable for high-fidelity analyses employing up to hundreds of analysis points.
SPARC’s MFTK is designed to quickly compute accurate performance with data from all levels of fidelity using a Hierarchical Kriging Interpolation algorithm. Generally, the methods utilize the trend information at lower-fidelity levels and anchor these trends to high-fidelity data. Thus, a full aerodynamics model for a vehicle can be achieved through a small number – typically fewer than one hundred – of high-fidelity points, anchoring thousands or more of low- and mid-fidelity points. This can cut the time to solution of such a model from months to just a couple of weeks.
Future plans for SPARC include further development of the MFTK to incorporate fast-running thermal response tools, including the 1D SPARC ablation capability, for an end-to-end one-way coupled aero/thermal analysis capability. This coupled aero/thermal analysis capability will replace existing legacy aero-thermal tools that have been employed at Sandia for flight vehicle analysis for over 40 years. The new capability will modernize/parallelize/automate the simulation process and generate a common interface for each of the software tools.