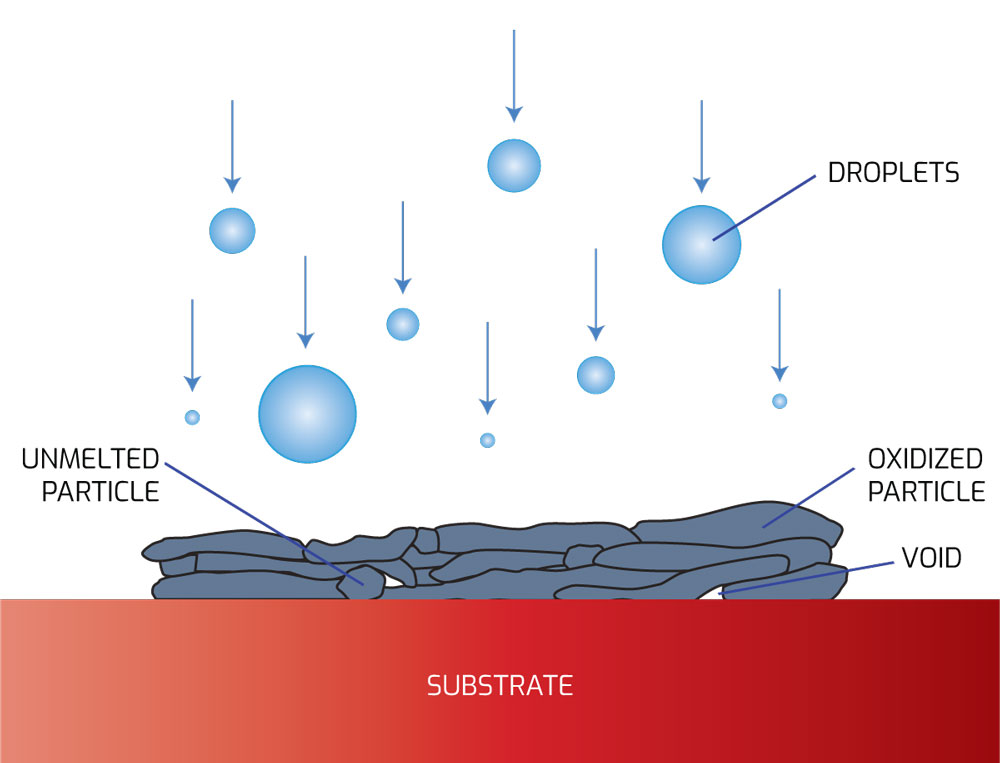
Thermal spray coating materials could help protect sensitive equipment and sensors at pulsed power, high energy-density facilities like Sandia’s Z machine from intense radiation, extreme heat and the flying pieces of debris generated during a shot. The ability to simulate how radiation and other thermally induced shocks travel through these spray-formed coating materials is important for understanding how the materials will perform and helps researchers analyze and design new coatings for next-generation pulsed power, inertial confinement fusion and other high energy density physics facilities.
Until now, previous quasistatic radiation transport simulations modeled just a subset of the physics occurring during a shot, showing researchers how much energy would be absorbed at any one point in space in the material, but unable to account for all aspects of the radiation environment. These old simulations also treated the spray coating material as a solid block of homogeneous material that didn’t fully capture the details of its structure. When the coatings will be sprayed on equipment, metal droplets will impact, solidify and deform on a substrate and form a porous, layered surface comprised of blobs of metal and small pockets of air, not a solid homogeneous material.
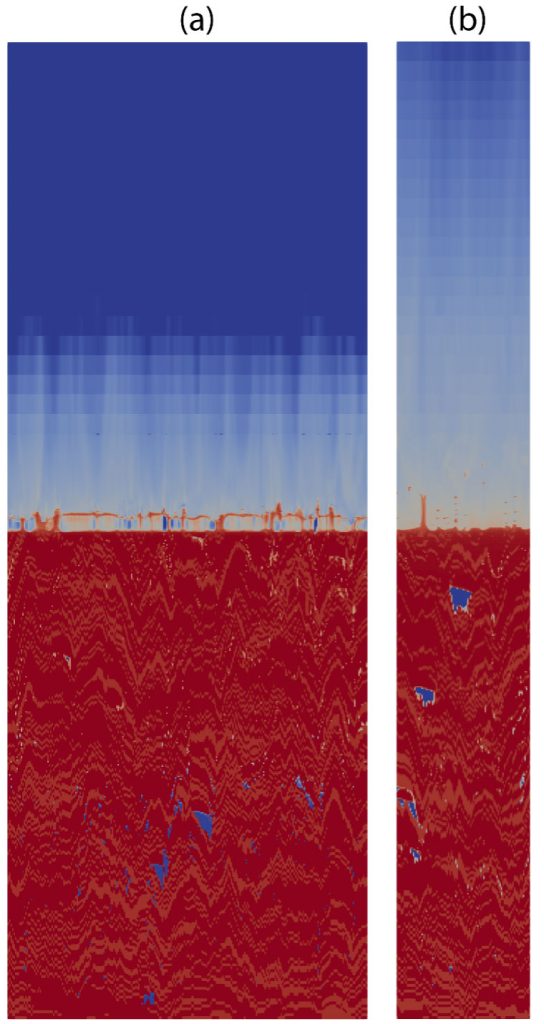
Using Sandia’s multiphysics code ALEGRA, researchers have developed fully coupled radiation hydrodynamic simulations that model radiation-induced shocks traveling through the heterogeneous mesoscale structure of spray-formed materials. These HPC simulations solve equations that include the physics of both radiation transport and solid dynamics to predict how the material would evolve in harsh environments.
Because these high-fidelity physics simulations now include mechanics – materials in motion and stress – the team can see, at any point in time and at any point in space, what the state of the material is, what the velocity of the material is, what the stress of that material is and what the energy is.
When a pulsed power facility like Sandia’s Z-machine fires a shot, the radiation that is produced and hits the equipment is so intense that it sends a stress wave through the material. These new advanced simulations show how the mechanical stress wave moves through the material, which is something the previous simulations couldn’t do. Researchers can predict stress wave profiles and mechanical surface phenomena when the system is placed in different facilities. This information can help researchers design a material that not only survives the intense environment but also reduces the stress created when the same radiation pulse is applied in the future.
To better model the spray-coating materials, the team generated representative volume elements of the mesoscale geometry of the coatings by using Sandia’s SPPARKS Kinetic Monte Carlo Simulator with an algorithm that mimics real structures generated by the spray process (Figure 1 and Figure 2). ALEGRA couples with the Kull IMC and SCEPTRE radiation transport codes to do radiation hydrodynamics simulations of the stress waves generated when the spray-coated material is subjected to photon and electron radiation environments in pulsed power facilities such as Z, the National Ignition Facility and Saturn. The insights from these simulations and experimental observations could help researchers design effective debris and thermal protection systems for these facilities.
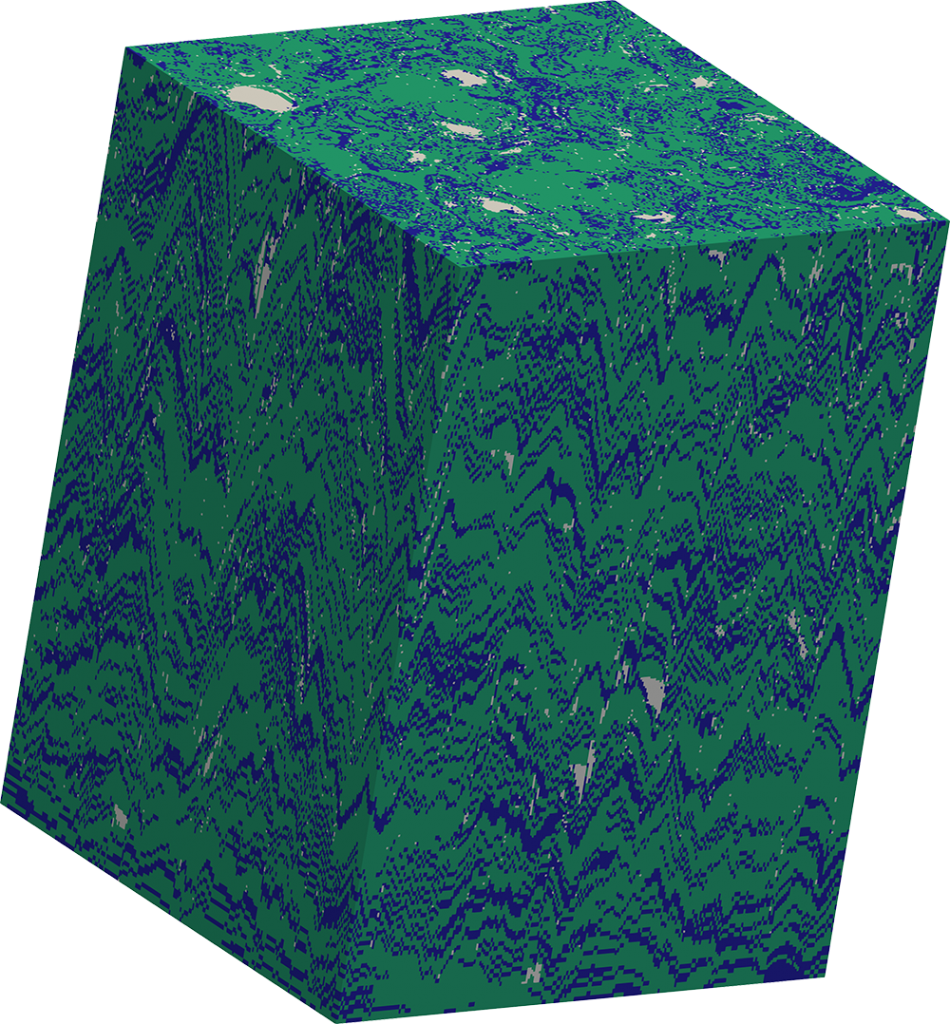
geometry is a roughly 0.7 x 0.7 x 1.0
mm representative volume element
containing metal “splats” (blue and
green) and air-filled pores (light gray).
In addition to their use in pulsed power facilities, refractory metals could potentially be used in inertial or magnetic confinement fusion applications, such as tokamak reactors, owing to their high temperature and corrosion resistance. The advent of spray-coating technologies and the ability to better simulate and analyze them could lead to these materials being used on reusable or even disposable machine components.
For future improvements, the team is working on improving the fidelity of the models to capture more of the relevant physics, including the interaction of stress waves with microcracks and better material model calibration for the constituent materials, whose material properties can differ from their non-sprayed counterparts.
This work was funded by NNSA’s Engineering and Technology Maturation program and Sandia’s Laboratory Directed Research and Development program.
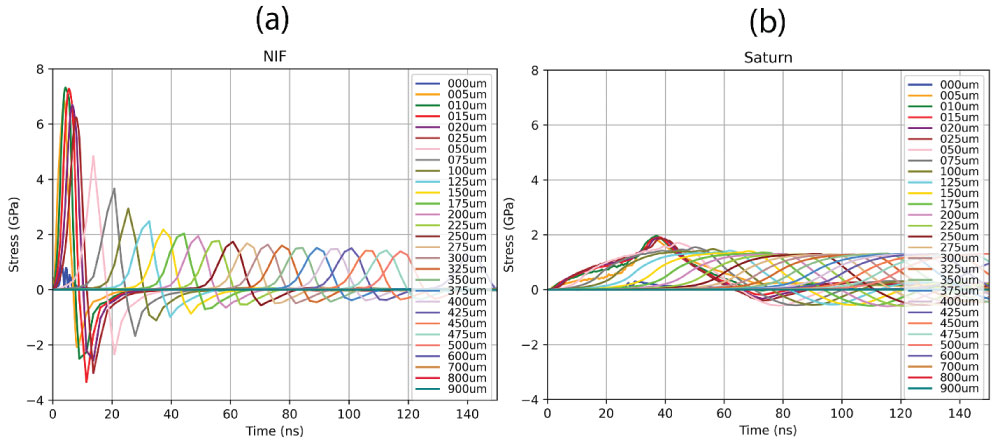