Sandia offers first class to aircraft industry to improve inspection of solid-laminates
See also: Airworthiness Assurance Center projects focus on composites
As manufacturers build more wings, fuselages, and other major parts of commercial aircraft parts out of solid-laminate composite materials, Sandia has shown that aircraft inspectors need training to better detect damage in these structures.
So the Airworthiness Assurance Center — operated by Sandia for the Federal Aviation Administration (FAA) for the past 26 years — has developed the first course to train inspectors in the airline and aircraft manufacturing industries nondestructive inspection techniques (NDI) for solid-laminate composite materials.
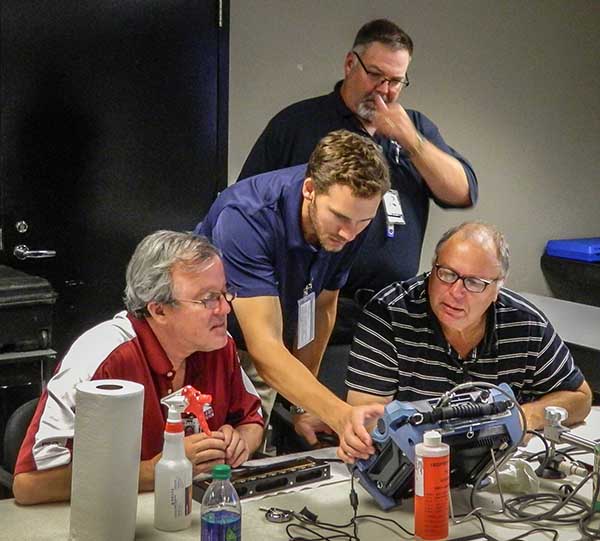
Stephen Neidigk (6626), center, a principal developer of the Composite NDI Training Class, teaches inspectors in the course at Delta Air Lines in Atlanta this summer. (Photo courtesy of Sandia National Laboratories)
The course was first presented this summer at Delta Air Lines in Atlanta, Georgia, to 35 engineers and inspectors from six countries. The FAA sponsored development of the course, which is now available to private industry.
“We’re trying to improve the proficiency of these inspectors so that they’re better able to detect damage in composite structures,” says Dennis Roach, a senior scientist in the Transportation, Safeguards & Surety Program (6620). “We’re also trying to increase the consistency in inspections across the commercial airline industry.”
By volume, 80 percent of the Boeing 787 and more than half the Airbus 350 by weight are made from composite materials, driving the need for this training, says mechanical engineer Stephen Neidigk (6626), a principal developer of the Composite NDI Training Class.
Alex Melton, a Delta manager of quality control and nondestructive testing, says the course began at the right time for his company. Delta will receive the Airbus 350 aircraft next year and the Bombardier C-Series shortly thereafter. Delta plans to have a customized version of Sandia’s course in place for its inspectors.
“This type of class enhances inspector proficiency insofar as it develops the skill of the inspectors,” Melton says. “I think it’s going to be a really good curriculum for our inspectors as we develop the training and integrate it into our training program and, certainly, I think it’s going to be valuable to the greater industry.”
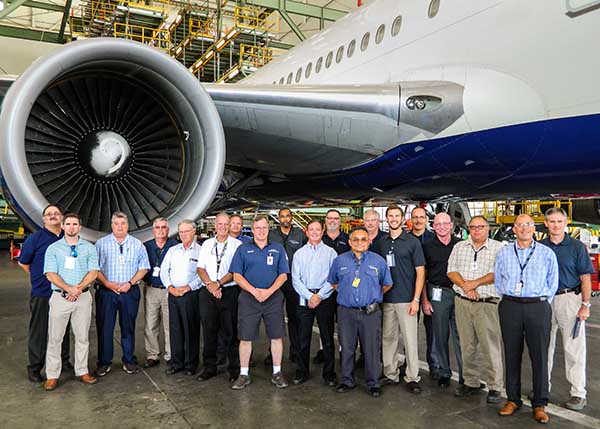
Participants take a break at the Composite NDI Training Class to gather in front of a Boeing 767 wide-body aircraft in a maintenance hangar at Delta. (Photo courtesy of Delta Air Lines)
Experiments detecting composite damage showed need for inspector course
For the past decade, researchers have conducted experiments on the probability of detecting damage in composite materials — honeycomb and solid-laminate structures — that showed wide variations in inspectors’ abilities and techniques, Dennis says.
Because many experienced aircraft inspectors started their careers when airplanes were made mainly of aluminum and because composites behave in so many different ways from metal, Sandia recommended the training.
They needed customized training that didn’t exist.
“We saw people not using the exact equipment setup, procedures, or methods that would produce optimum inspection results,” Dennis says. “They needed customized training that didn’t exist.”
Building on that recommendation, Sandia conducted two workshops in 2014-15 involving regulators, airlines, and aircraft manufacturers from 12 countries to refine the course content. The FAA also provided feedback on the course and the design of the NDI Proficiency Specimens used in the hands-on portion of the class, Dennis says.
The two-day course covers the properties of composites, the manufacturing processes, and the benefits and shortcomings of the materials. Composites produce more fuel-efficient aircraft because they are lighter than metal. Due to the materials’ structures, they are resistant to fatigue and do not crack as easily as metal, in part because they use fewer joints and fasteners where cracks can originate. But one drawback is that solid-laminates can suffer damage, particularly from impact, that’s not visible at the surface, often because the visible, external surface pops back into place, masking subsurface damage, Dennis and Stephen say.
Sandia’s Laboratory Directed Research and Development program sponsored two research projects on the structural health monitoring of composite materials and the development of sensor network systems to assess damage in transportation infrastructure. These studies produced information that was useful in the development of the course.
Engineered damaged parts based on years of research help inspectors practice
In the course, inspectors learn about nondestructive testing techniques through hands-on exercises. They examine custom carbon-fiber composite samples representing various types of structural configurations common on aircraft, but including engineered defects that range in complexity to fine tune their skills, Stephen says. The samples were designed and built by Sandia and aerospace company NORDAM, based in Tulsa, Oklahoma, based on years of Sandia research.
The inspectors set up commercial scanners, including phased-array ultrasonic scanners where they “paint” a two-dimensional image of the composite with ultrasound (C-scan image) to detect damage, and learn to optimize the settings to more clearly detect damage, Stephen says.
They learn how to recognize structural features found in composites, including laminates with substructure such as co-cured bond lines, tapered laminates, and others, and types of damage, including disbonds, delamination, porosity, and impact damage.
The airline industry wants to save time and money by reducing “false calls,” when inspectors believe they have found signs of damage that is not actually there. An eye-opener for course participants was noticing that the scanner signals decreased in amplitude or intensity due to the presence of acoustic tiles and sealant accompanying composite fuselage panels. These are commonly used to mitigate aircraft vibration noise for passengers. The poor readings on the detection equipment might appear as damage to an untrained inspector, Stephen says.
But with practice, Melton says, the inspectors learned to discern the effects of the acoustic tiles on the signals generated by the defects.
One of the most valuable things in our view about this class was the opportunity to practice with these materials . . .
“One of the most valuable things in our view about this class was the opportunity to practice with these materials because we really don’t get that opportunity and feedback on the aircraft,” he says.
In preparing the course, Sandia engineers recorded the best results they obtained in the lab to identify flaws in the engineered samples and produced flaw maps and grading templates, Stephen says.
“After the participants have the chance to inspect the panels, we use our grading templates to point out which ones they hit and missed. Then we show them how the reflected signal changed for a particular flaw and why they missed it,” he says.
Dennis and Stephen expect that companies will customize the course, as Delta did, to meet their needs and they will support those efforts as necessary. The team hopes to develop further nondestructive testing courses, particularly to inspect composite aircraft repairs, Dennis says.
Airworthiness Assurance Center projects focus on composites
The Airworthiness Assurance Center currently has several projects funded by the FAA to study composite materials used on aircraft in addition to the training program, says mechanical engineer Stephen Neidigk.
In a composite impact project, the team is looking at how solid-laminate composite structures respond to high-speed hail and “rigid-body impacts,” such as damage from baggage handling equipment or being hit by dropped tools.
To study hail impact, the researchers used a high-velocity, compressed-air gas gun at the University of California-San Diego to shoot 2.4-inch diameter ice balls at full-scale composite fuselage panels containing substructure elements at different velocities to characterize hail damage. They then applied nondestructive inspection (NDI) methods to assess sensitivity and deployment on large structures. Some results from these studies were included in the Composite NDI Training Class.
The Airworthiness Assurance Center team also is working on a separate project looking at the integrity of aged repairs on flight control surfaces. These components are typically “sandwich composites,” which contain honeycomb structures enclosed in aluminum or other “skins.” Sandia worked with the FAA and industry partners to locate retired aircraft that had repaired components with long flight histories. The components were removed from the aircraft and investigation is under way to determine how the repairs have held up over time, Stephen says.
The project is being done with Wichita State University, which is conducting full-scale structural tests on these components to look at the damage tolerance of these repairs to see how well they’ve lasted.