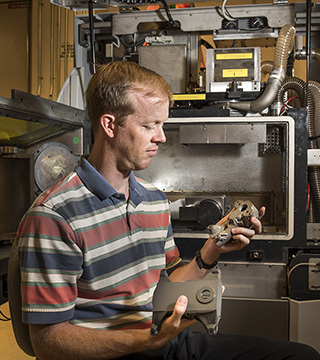
MATERIALS ASSURANCE — Bradley Jared (1832) sits in front of a new selective laser melting machine at Sandia for metal additive manufacturing (AM) as he holds two prototype housings designed through a technology called topology optimization. Sandia researchers who are exploring additive manufacturing for nuclear weapons and other national security needs say they need to understand how AM processes affect the properties of materials that are generated. (Photo by Randy Montoya)
Sandia researchers are exploring how to use additive manufacturing, familiar to most people as 3-D printing, to make parts for nuclear weapons and other national security needs, saving time and money and simplifying the manufacturing process.
The target of much of its research is an advanced metal additive process that uses a laser to melt successive layers of metal powder to build up shapes. The technique lets engineers design in ways that aren’t possible with standard manufacturing methods and could make components that perform better and weigh less. But researchers must answer hard questions before they can certify that parts made in non-traditional ways can meet high-consequence requirements.
President Barack Obama has pushed for ways to strengthen US manufacturing. Last year, Sandia joined America Makes, the federally backed National Additive Manufacturing Institute, which aims to reduce the cost of 3-D printing, offer new opportunities to businesses, and train American workers in sophisticated technologies. Ultimately, a robust additive manufacturing industry could make the nation more competitive in a global market.
Additive manufacturing opens up seemingly limitless possibilities. It can make shapes with complicated geometries that traditional machining can’t handle. It offers the potential to integrate parts or assemblies, reducing the number of joints and other interfaces that could be points of failure. In the future, designers might be able to custom-tailor the properties of additive materials to make components better. All of those opportunities could save both time and money.
Understanding properties of new materials
The biggest barrier to using new materials is understanding their properties well enough to certify that they meet rigorous requirements for high-consequence applications. Materials assurance, a key to certification and qualification, is “the first, most immediate obstacle that we need to overcome,” says manager Andre Claudet (2617).
Parts must meet multiple requirements for mechanical, thermal, or vibration performance — particularly crucial when something is intended for a nuclear weapon, a satellite, or an airplane. “How do you actually verify the material is what you want? For some applications it’s not a big deal. For high-consequence hardware it’s a very big deal,” says Bradley Jared (1832).
The path to certification requires conducting experiments using instruments to understand what’s happening and performing sophisticated computations to verify that material properties meet specifications.
Sandia is well-suited to tackle the problem because of its expertise in computational mechanics and analysis, high-performance computers, and modeling tools it developed. Sandia also has experience in handling large amounts of data, people who know how to write and adjust codes, skill in materials science, and a history of inventing additive manufacturing techniques. In the 1990s, Sandia developed both Laser Engineered Net Shaping (LENS), a process to print complex metal parts from powders, and robocasting, a 3-D ceramic process that forces ceramic slurry through a pressurized needle to create a part that is fired in a furnace to harden it. Both processes have been commercialized.
Most metal additive techniques involve melting a feedstock material that then re-solidifies into its final shape. However, the process alters a material’s microstructure, which can dramatically affect its properties and how parts perform. Researchers need to understand how the extreme temperatures and heating and cooling rates affect material properties.
Metal parts historically have been made from ingots, rods, bars, or plates whose properties can be verified. “You can cut some samples and check the chemistry and the microstructure and mechanical properties and say, ‘Yea verily, this is a good piece of material and anything you make out of it will be fine,’” says Senior Manager Mark Smith (1830). “With additive you build material at the same time you build the part. So the question is, does it have the right microstructure and chemical composition and are there defects like voids or unmelted particles that will affect its performance?”
Strength, other characteristics affected by how materials are processed
Important material characteristics such as strength or ability to withstand stress depend on many things, including how a material’s internal structure is affected by phase changes — for a simple analogy, think ice melting into water, then refreezing into ice again. In the laser metal powder bed process, for example, feedstock powder is random in the way it’s laid down and in its distribution of particle sizes. As the laser scans the surface and melts some particles, they coalesce.
“The behavior of the final part depends on the metallic microstructure of the material from which it is built,” says manager Anthony Geller (1516), whose department does modeling and simulation for fluid and multiphase flows. “The microstructure depends on the temperature history that the metal experienced while it was cooling, and the temperature history the metal experienced while it was cooling depends on the temperature and flow history of the particles as they were heated, melted, and flowed together, which in turn depends on that first step, how the particles were laid down.”
Anthony says researchers must acknowledge the inherent variability of additive materials, and design according to probabilities for internal stress.
Embracing material variability is the broader goal of Sandia’s Engineering of Materials Reliability Research Challenge, which is developing a framework to understand how variability impacts the reliability of engineering components. The research challenge is using the metal additive process for its initial study.
Additive manufacturing allows designers to create complex geometries that can’t be made by traditional manufacturing. Given the triple constraints of cost, schedule, and performance, a complex part can be preferable: it’s cheaper because you use less material and faster because you’re printing less, and it performs better because optimization tools are used, Andre says. Sandia is developing computational tools incorporating technologies such as topology optimization (see story on next page) to take advantage of this aspect of additive manufacturing, he adds.
But it’s very difficult to characterize complicated additive manufacturing parts such as a bar engineered for rigidity that resembles the skeleton of a cholla cactus. “From a production standpoint that’s the part I want to make because it’s faster and uses less material,” Bradley says. “From a measurement standpoint, however, that part is a greater challenge.”
Research must measure temperatures as structures form
For accurate simulations, researchers must know what happens as layers are put down, but it’s difficult to measure temperatures in layers that become hidden as other layers form on top. “We can’t embed anything in those lower layers because that would change the behavior,” Anthony says.
Simulations, aimed at calculating real-world results using large computers, can predict temperatures in inaccessible layers, while experiments can validate the model. Simulations can study parameters such as particle size distribution that would be difficult and costly to study by experiments alone.
Diagnostics for the LENS process included a thermal camera to learn about the melting process and metallurgy, and Bradley suggests something similar for the powder bed process. Some studies have used optical cameras to see how the powder disperses on a layer and to study the powder laydown process. Some diagnostics might be able to use these types of sensors.
“Right now we don’t have a whole lot of information coming off the machine and off the process,” Bradley says. “We don’t know what we don’t know.”
Understanding how materials form might eventually mean custom-tailoring microstructure properties.
“So you can have different material, different microstructures, different properties in different regions that can be incorporated as part of the design process if we can understand it well enough,” Mark says. “That’s sort of the long-term vision: You would not only design the geometry, but actually design the microstructure of the part as you build it.”
Additive manufacturing is a tool, not a panacea, and won’t replace traditional manufacturing for everything, he says. “We’re not going to print a complex mechanical assembly with precision moving part anytime in the near future,” he says. “But there may be some applications where it offers unique advantages for us.”
Bradley expects it to complement current techniques. “Where you need it, you’ll use it, and where you don’t, you’ll use traditional methods.”