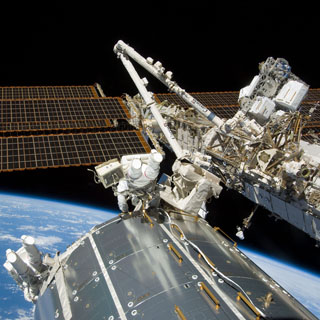
Sandia-developed satellite systems have increased their sensing capabilities dramatically in recent years, but the bandwidth available for these payloads to transmit data to Earth has essentially remained constant, creating a kind of data logjam.
The Sandia solution has been to prereduce the large data stream by developing processing architectures that increase satellite onboard computing capabilities. Then, only the most useful information would be transmitted to Earth.
ASTRONAUTS deploy passive experiment containers (PECs), including MISSE-7, during an EVA outside the International Space Station. (NASA photo)
But questions as to how well the latest in computing electronics would fare in the harsh environment of outer space, where high-energy particles might collide with a transistor and change the value of an individual calculation, remained unresolved.
Now, preliminary results of a Sandia experiment in progress on the International Space Station are providing insights into the effects of high-energy radiation on these computing electronics, enabling appropriate mitigation of these potentially crippling effects in future Sandia designs. “We’re getting true on-orbit data from a space environment,” says Dave Bullington (2664), Sandia’s lead engineer on the experiment taking place in low Earth orbit.
NASA’s “Materials on the International Space Station Experiment” (MISSE) program, under the direction of the Naval Research Laboratory (NRL), provides opportunities for low-risk, quick and inexpensive flight tests of materials and equipment in space aboard the International Space Station (ISS), says NRL lead Robert Walters.
Passive experiment containers hold multiple experiments
MISSE provides suitcase-like containers called passive experiment containers (PECs) to hold multiple experiments. These are mounted by astronauts on the exterior of the ISS, thus exposing the experiments to the rigors of space.
The seventh in an ongoing series of MISSE flight opportunities, MISSE-7 for the first time offered researchers power and data connections provided by the ISS from which to run actively powered experiments.
On Nov. 16, 2009, the space shuttle launched carrying the MISSE-7 equipment and on Nov. 23, astronauts manually deployed these containers on the exterior of the ISS. Sandia has been receiving data from this research payload ever since.
At the heart of these new computing architectures are powerful yet flexible computing chips, configurable to support different missions. These chips are called reconfigurable field-programmable gate arrays (FPGAs).
Reconfigurable field-programmable gate arrays
Since these FPGAs are reconfigurable rather than limited to a predefined architecture, their circuits can be overwritten, somewhat the way a read-write compact disk has more possible uses than a read-only disk. This makes prototyping easier and also permits changing missions on satellites previously designed for other purposes. Because new generations of FPGAs available from commercial suppliers may not have been fully tested for reliable performance in space, Sandia engineers help validate device performance in a relevant environment before the devices are integrated into high-consequence operational systems.
Sandia, in a partnership with Xilinx, designed the SEU Xilinx-Sandia Experiment (SEUXSE) for this opportunity to fly on MISSE-7. (SEUs — single event upsets — refer to electronic changes caused by collisions with a single subatomic particle.)
SEUXSE contains a fourth-generation space qualified FPGA (Virtex 4) and a fifth-generation commercial or non-space qualified FPGA (Virtex 5) from Xilinx. Converting the ISS power to levels compatible with the Virtex devices are Sandia-designed power converters known as point-of-load (POL) converters.
Sandia engineer Brandon Witcher (5762) provided the POL design for SEUXSE — the first time these efficient, high-quality power converters have been used in space.
Special algorithms were developed and programmed into both of these Virtex FPGAs to detect and report upset events while the FPGAs were running typical satellite data-processing tasks. Dave notes that each Virtex contains two traditional processors in addition to several other circuits designed to capture upset performance data relating to each circuit type. “We’re validating models with four computers inside these chips and sending back data messages every few minutes.”
With the data collected from this platform, researchers in future Sandia programs will know exactly how these FPGAs and POL converters perform in the space environment and how to design mitigation approaches into these processing routines to account for upsets encountered in space.
SEUXSE II
A second experiment called SEUXSE II, featuring even more recent computing components, has already been prepared to lift off on a future shuttle flight as part of MISSE-8. For SEUXSE II, Sandia researchers replaced the commercial version of the Virtex 5 from Xilinx with an early release version of the space-qualified Virtex 5.
“Fortunately,” says SEUXSE researcher Jeff Kalb (2664), “the new Virtex 5 from Xilinx had a compatible footprint to the previous Virtex 5 and we could leverage the hardware that was designed for MISSE-7.”
Sandia researchers were also able to expand on the algorithms designed for MISSE-7 to provide even more insight to the space environment on MISSE-8.
SEUXSE II was delivered to NRL on Feb. 1, 2010, and MISSE-8 is expected to launch on the Space Shuttle in July 2010. When it is deployed on the ISS, it will replace the MISSE-7 PEC, which will be returned to Earth on the shuttle, allowing Sandia researchers to analyze SEUXSE hardware after it has been on orbit.
Sandia is the first to put these versions of the Virtex technology into orbit, Jeff says. These FPGAs and POL converters likely will become the heart of future processing architectures for Sandia’s DOE/NNSA customers. “The point is for us to get early on-orbit information on how these devices function in space.”
The mechanical design of SEUXSE and SEUXSE II was achieved by Dennis Clingan (2617), experienced in designing packages for NASA programs where astronaut safety is paramount.
Testing materials in the harsh space environment MISSE-7 is also flying the Sandia Passive ISS Research Experiments (SPIRE). These tests passively expose a variety of materials and devices to the harsh space environment. Upon return to ground, they will be tested to determine if degradation has occurred due to synergistic factors such as ionizing radiation, UV exposure, thermal cycling, micrometeorite impacts and vacuum effects. Radiation-shielding structural composites (Dave Calkins, 1833 and Gayle Thayer, 5711), doped laser fibers (former Sandian Dahv Kliner), pure tin finished parts (Ed Binasiewicz, 5761), MEMs latching impact sensors (Mike Baker, 1749), and GaAs photodiodes (Alan Hsu, 5719) are some of the 15 Sandia passive experiments that together are SPIRE.
Sandia, through the support of the NA-22 Space Nuclear Detonation Detection (SNDD) Program office, developed SEUXSE and SPIRE in an 18-month period for a cost that was one-fifth of other comparable experiments. SEUXSE II was then delivered in one-third the time and cost of the original SEUXSE.
Additional help was given by Gayle Thayer (5711), who is the principle investigator and primary interface with NRL; Tracie Durbin (1513), who provided thermal analysis; Ethan Blansett (5735) who provided space radiation environment modeling and upset rate predictions; Mythi To (5337), who provided SEUXSE hardware design support; Dave Heine (2664) Jonathan Donaldson (2664), Chris Wojahn (5337), Dave Lee (2664), and Jim Daniels (5337), who developed the algorithms and provided test support for SEUXSE; and Org. 5761, which provided fabrication support.