
Sandia Robotic Hand
The unique Sandia robotic hand, developed in collaboration with Stanford University and Lunar for the DARPA-sponsored Autonomous Robotic Manipulation (ARM) program, is a low-cost, highly dexterous, modular unit that can support a wide variety of applications ranging from counter-IED and Explosive Ordnance Disposal to Search and Rescue as well as work in Extreme Environments. Approximately 50% of the components in the Sandia Hand are 3D printed.
Multi-focal Telescope
A Sandia team designed and built this multi-focal telescope to demonstrate how to design and manufacture taking into consideration both the strengths and weaknesses of additive manufacturing. The final assembly includes more than 80 AM components with an additional 20+ parts printed for tooling, fixturing, and development hardware. It is estimated that it was completed in 1/3rd the time and 1/5th the cost of building such a prototype in the traditional way.


SpinDx
Sandia researchers have developed a break-through technology which can test and diagnose up to 64 medical assays on a single disc within 15 minutes of sample collection. It requires significantly less blood (less than a pin-prick) than the current laboratory blood draw. This device can revolutionize the way doctors and hospitals get blood test results.
BaDX
Sandia’s credit-card-sized anthrax detection cartridge aids global agriculture and is recognized with multiple 2015 national awards including an R&D100 award, TechConnect Innovation award, and the Federal Laboratory Consortium’s award for Excellence in Technology Transfer.


Sandia Rockets
Sandia is using AM to accelerate the design to production cycle time and reduce costs. Metal AM parts used in Sandia rockets, such as the one shown here being launched from Sandia’s Kauai, Hawaii, test faciltiy, have resulted in estimated time and cost savings on the order of 60%, while also providing real world flight experience with AM hardware.
Printed Wind Turbine Blade Mold
Sandia National Laboratories, Oak Ridge National Laboratory, and TPI Composites partnered on the production of 3D printed molds for subscale developmental wind turbine blades. Compared to conventional methods, which are very expensive and time-consuming, this production technique allows for rapid, cost efficient construction of new wind blade designs. Sandia and ORNL won a Federal Laboratory Consortium Regional Partnership Award in 2017 for this work. (Photo courtesy of Brittany Cramer, Oak Ridge National Laboratory)

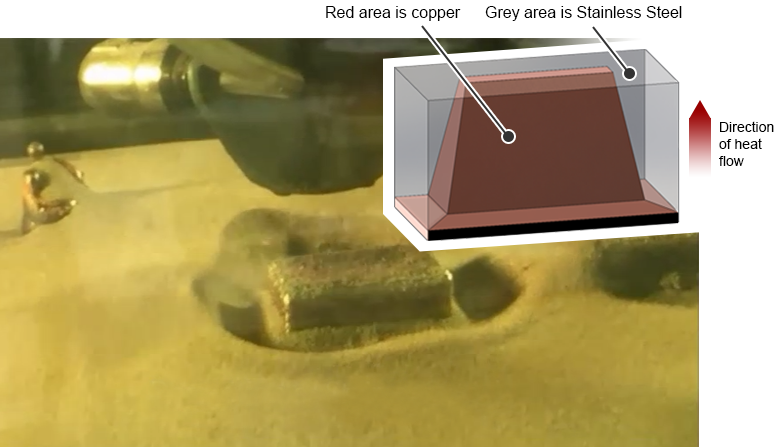
3D Printed Bi-Metal Thermal Concentrator
Sandia invented one of the first metal AM technologies, LENS (Laser Engineered Net Shaping), in the mid-1990s. A major advantage LENS for some applications is the ability to print more than one metal in a single part with either sharp or graded interfaces between the different metals. In the example below, a wedge of high-thermal-conductivity copper is 3D printed within a realtively low-conductivity stainless steel "shell" to create a thermal energy concentrator.