My research focuses on complex multi-scale, multi-physics model development and analysis for national defense and industry multi-mechanics problems. I am a developer of the mechanics codes GOMA and SIERRA, and I use these codes to address problems in complex coupled multi-mechanics (fluid, solid, thermal, electromagnetic). Much of my research involves understanding interfaces, where I work with ALE and level-set methods, and with reduced-order models, such as lubrication and thin-film flow. I also focus on highly-coupled problems involving fluid mechanics, solid mechanics, thermal transport, and species transport. Applications range from weapons systems and components to battery materials.
Current Projects
Credible Automated Meshing of Images (CAMI)
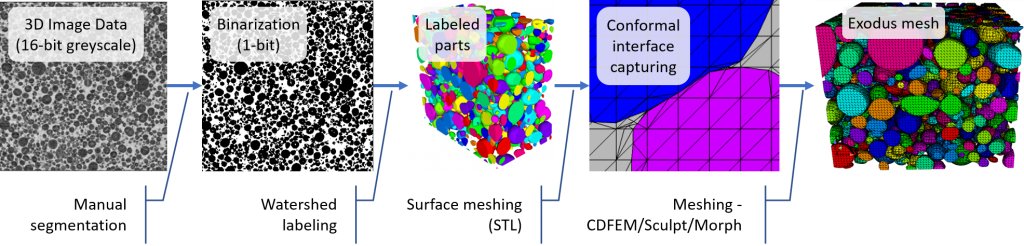
Discretized geometric representations (i.e. meshes) are foundational to computational simulation, yet typically: (1) are based on simplified geometric descriptions, not as-built parts; (2) require the most manual labor of the analysis process; and (3) display analyst-to-analyst variability with unquantified uncertainties. In this Laboratory Directed Research and Development (LDRD) project, will are researching/developing novel deep learning (DL) algorithms to convert greyscale 3D tomographic scans into sharp geometries with quantified geometric uncertainties. Computational meshes for multi-physics simulations will be efficiently generated and geometric uncertainties will be propagated through to performance predictions. Success will increase confidence in stockpile safety/security by enabling efficient creation of serial-number-specific digital-twin models directly from 3D imaging.
The techniques developed in this project will be applied to a wide range of applications, including thermal protection system (TPS) materials, battery electrodes, detonators, and more. Applications span length scales, from material microstructures to components and systems.
M. C. Krygier, T. LaBonte, C. Martinez, C. Norris, K. Sharma, L. N. Collins, P. P. Mukherjee, S. A. Roberts, "Quantifying the unknown impact of segmentation uncertainty on image-based simulations," Nature Communications 12 (2021) 5414, DOI: 10.1038/s41467-021-25493-8
S. A. Roberts, H. Mendoza, V. E. Brunini, D. R. Noble, "A verified conformal decomposition finite element method for implicit, many-material geometries," J. Comp. Phys. (2018) DOI: 10.1016/j.jcp.2018.08.022
Mesoscale Modeling of Li-Ion Battery Materials
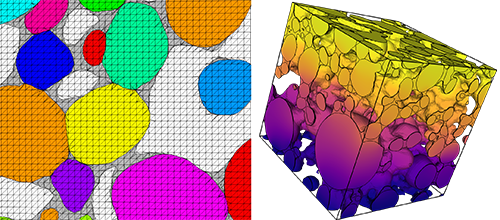
Lithium-ion battery electrodes are typically designed using an iterative, experiental process, where electrodes are manufactured and tested in cells, without necessarily understanding how the manufacturing conditions impact the electrode mesosctructure. It is the coupled thermal, electrochemical, and mechanical interactions of the electrode active particles, conductive binder domain, and electrolyte at the mesoscale that governs the effective properties, electrochemical performance, and degradation mechanisms of the electrode.
In this project, we develop the computational capabilities and mathematical models to study lithium-ion battery electrodes at the mesoscale. Our simulations are based on 3D imaging of the electrode mesostructure, typically through x-ray computed tomography (CT), and often capture thousands of particles in a single domain. The computational models include mechanical deformation and cracking, species transport, electrochemical swelling, and thermal effects. We also simulate the manufacturing of battery electrodes using discrete element method simulations and study both intercalation and conversion electrodes.
This work was initially funded by Sandia’s Laboratory Directed Research and Development (LDRD) program and is now funded through the CAEBAT program of DOE’s Vehicle Technology Office.
I. Srivastava, D. S. Bolintineanu, J. B. Lechman, S. A. Roberts, "Controlling Binder Adhesion to Impact Electrode Mesostructure and Transport." ACS Appl. Matls. & Int. (2020) DOI: 10.1021/acsami.0c08251
M. E. Ferraro, B. L. Trembacki, V. E. Brunini, D. R. Noble, S. A. Roberts, "Electrode Mesoscale as a Collection of Particles: Coupled Electrochemical and Mechanical Analysis of NMC Cathodes," J. Electrochem. Soc. (2020) DOI: 10.1149/1945-7111/ab632b
B. L. Trembacki, A. N. Mistry, D. R. Noble, M. E. Ferraro, P. P. Mukherjee, S. A. Roberts, "Mesoscale Analysis of Conductive Binder Domain Morphology in Lithium-Ion Battery Electrodes," J. Electrochem. Soc. (2018) DOI: 10.1149/2.0981813jes
Battery Performance Modeling
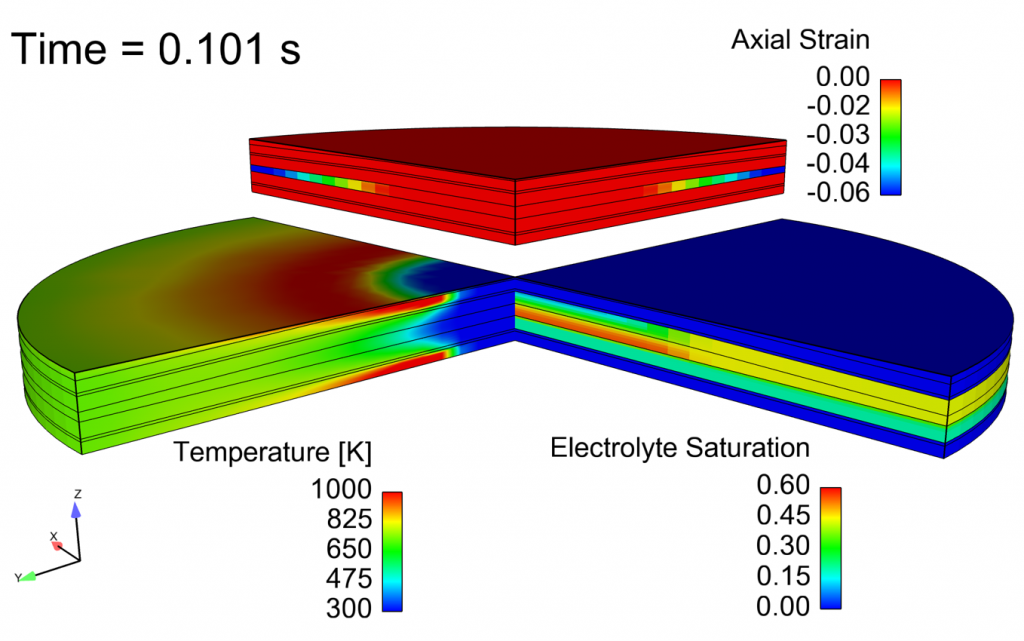
I lead a team of engineers developing coupled, multi-physics simulations of battery performance, primarily molten salt batteries. These models range in scale from the single-cell level (shown in the figure), to full battery battery stacks, and even to the integration of batteries into sub-assemblies. Our models capture a variety of physical phenomena, including heat generation and transport, phase change, fluid flow through porous media, solid deformation, species transport, electronic transport, and electrochemical reactions. We have established the credibility of these models through rigorous verification, validation, and uncertainty quantification (V&VUQ) practices.
Our expertise is in carefully coupling the physics to obtain numerical stability while optimizing computational cost. Our models are wrapped in a specialized GUI and delivered to the desktops of battery designers. Much of this work is funded under the National Nuclear Security Administration’s Advanced Simulation and Computing Physics and Engineering Models initiative and the DOE/DOD Joint Munitions Program.
More recently, we have been extending our expertise towards alkaline and lithium-ion chemistries through the Department of Energy’s Computer-Aided Engineering for Electric-Drive Vehicle Batteries (CAEBAT) program. Many of the electrochemical modeling capabilities generated for molten salt batteries have been reapplied to lithium-ion batteries and implemented in the CAEBAT codes.
T. G. Voskuilen, H. K. Moffat, B. B. Schroeder, and S. A. Roberts, "Multi-fidelity electrochemical modeling of thermally activated battery cells," J. Power Sources (2021), doi: 10.1016/j.jpowsour.2021.229469.
S. A. Roberts, C. F. Jove-Colon, H. K. Moffat, M. L. Neilsen, E. S. Piekos, B. B. Schroeder, B. L. Trembacki, T. G. Voskuilen, "TABS: A Thermal Battery Desktop Design Tool." Proceedings of the 48th Power Sources Conference (2018).
Thermal Protection System Materials
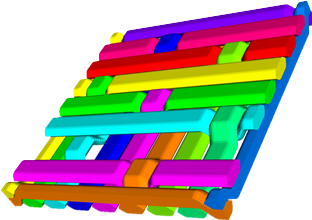
Space vehicles that enter the Earth’s atmosphere require the use of a thermal protection system (TPS) material to protect the reentry vehicle from the extreme temperatures generated during atmospheric flight at high speeds. A class of these materials pyrolize and ablate as a mechanism to remove heat, and predicting this ablation process is crucial for designing the TPS material.
We are developing transient mesoscale modeling capabilities to better understand and predict the fundamental processes at work during TPS ablation. These models resolve the TPS mesosturcture, which is often a woven composite, and capture physics including heat transfer, pyrolysis, gas flow, and mechanical deformation.
Photovoltaic Module Durability
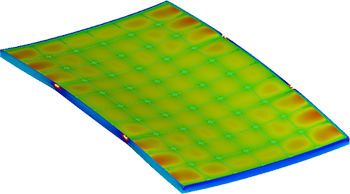
Under the DuraMAT program’s Predictive Simulation capability, we are developing coupled thermal, mechanical, and electrical models for the durability of photovoltaic (PV) modules. Our modeling is occurring at two length scales. First, the fine details of a single PV cell and the interconnects between cells are being modeled to understand how solder joints and other small features may cause stress concentrations and durability issues. Knowledge gained from this cell scale is then applied to the full module scale, where the module can be subjected to cyclical thermal, mechanical, or electrical loads to study durability.
Models are implemented in Sandia’s SIERRA Mechanics code and performed on various DOE high-performance computing clusters. The capability is being made available to the greater PV community through the DuraMAT program.
J. Y. Hartley, M. Owen-Bellini, T. Truman, A. Maes, E. Elce, A. Ward, T. Khraishi, S. A. Roberts, "Effects of Photovoltaic Module Materials and Design on Module Deformation Under Load," Journal of Photovoltaics (2020) DOI: 10.1109/JPHOTOV.2020.2971139
SIERRA Code Development
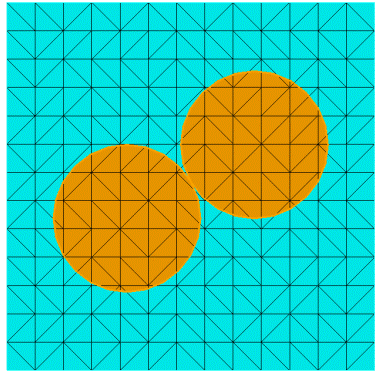
Developer in the thermal/fluids development team for the SIERRA Mechanics codebase, a flexible finite element method code written in C++. My efforts focus on supporting component design and analysis, including foam encapsulation, energetic materials, and battery modeling.
This work is funded under the National Nuclear Security Administration’s Advanced Simulation and Computing Integrated Codes initiative.
SIERRA Thermal/Fluid Development Team, "SIERRA Multimechanics Module: Aria User Manual – Version 4.54" Sandia Report, SAND2019-12296 (2019). DOI: 10.2172/1570564
Previous projects
Models for Nanomanufacturing
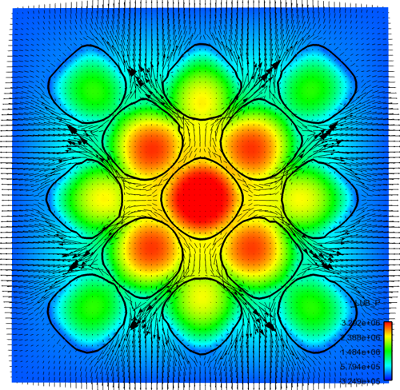
Developed reduced-order models for lubricating and porous flows with fluid-structural interactions for nanomanufacturing applications. The original focus was on Nano-Imprint Lithography. These models have now been deployed for a variety of other applications.
S. A. Roberts et al., "Multiphase hydrodynamic lubrication flow using a three-dimensional shell finite element method," Comput. Fluids, 87 (2013) 12-25. DOI: 10.1016/j.compfluid.2012.08.009. S. A. Roberts and P. R. Schunk, "A reduced-order model for porous flow through thin, structured materials," Int. J. Multiphase Flow, 67 (2014) 25-36. DOI: 10.1016/j.ijmultiphaseflow.2014.07.013.
Microfluidic Drop Dynamics
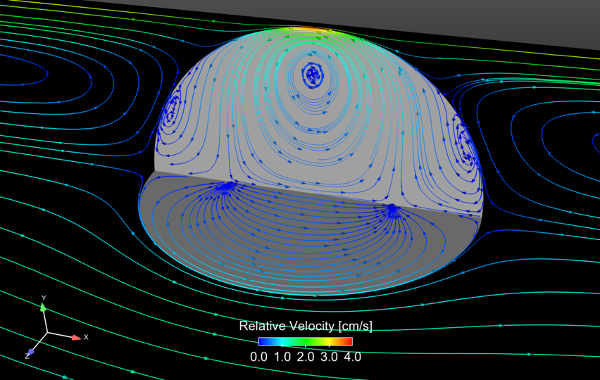
In collaboration with experimentalists, we have studied flow of microscale fluid drops through microfluidic devices. Level-set and CDFEM techniques were used to characterize the flow patterns withing drops, and we have used that knowledge to inform studies of mass transfer in microfluidic devices.
C. C. Roberts, S. A. Roberts, M. B. Nemer, and R. R. Rao, "Circulation within confined droplets in Hele-Shaw channels," Phys. Fluids 26 (2014) 032105-11. DOI: 10.1063/1.4867695.
Industrial Free Surface Flows
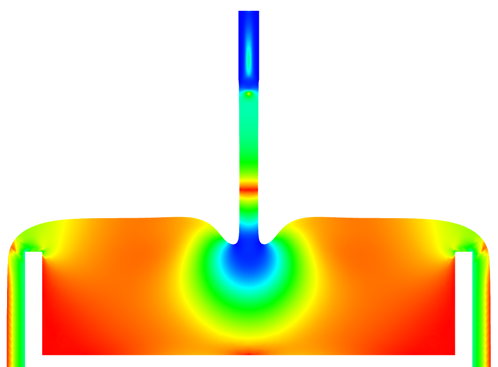
Properties of fluid-gas interfaces, such as surface tension and contact angle, can have a signficant impact on industrial processes such as bottle filling. We use the Goma and Sierra finite element codes to study these processes, finding optimal processing conditions. Our analyses range from axisymmetric steady-state, which allows rapid exploration of large parameter spaces, to fully-transient 3-D analyses, allowing exploration of detailed physics. Our studies have lead to increased process efficiencies, saving our partners signficant money.
S. A. Roberts and R. R. Rao, "Numerical simulations of mounding and submerging flows of shear-thinning jets impinging in a container." J. Non-Newtonian Fluid Mech. 166 (2011) 1100-1115. DOI: 10.1016/j.jnnfm.2011.06.006