Sandia tests nuclear battery safety for NASA’s Mars 2020 mission
Mars is really cold; at night it can get down to -130° F. The rover for the Mars 2020 mission, like Curiosity and other Mars rovers before it, needs a way to stay warm and continue exploring the Red Planet, even without sunlight.
Radioisotope thermoelectric generators, or RTGs, convert the heat produced by natural decay of radioactive materials such as plutonium-238 into electricity. The heat keeps the rover warm enough that its electronics and moving parts don’t freeze, and the electricity produced runs vital scientific instruments. RTGs have been used on space probes such as Pioneer 10 and 11, Voyager 1 and 2, Cassini, and New Horizons; the Apollo lunar experimental modules; and the Curiosity rover.
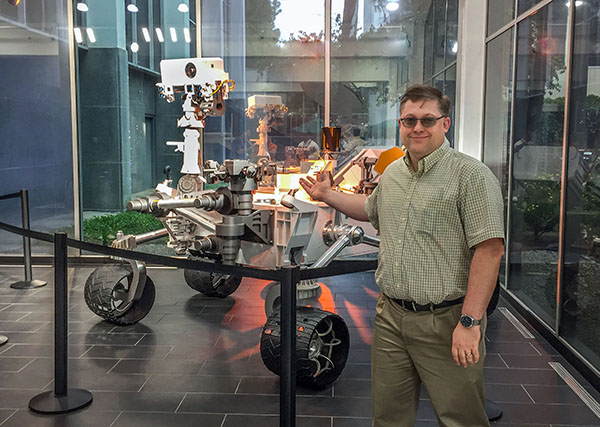
CHEMICAL ENGINEER Dan Clayton poses with a full-scale model of the Mars Curiosity rover at the Jet Propulsion Laboratory. Dan and his team assess the potential risks of accidents involving the Mars 2020 rover’s radioisotope thermoelectric generator battery. (Courtesy Dan Clayton)
In the unlikely event of an accident during the launch of the Mars 2020 rover, the fuel from the RTG has the potential to break through multiple layers of containment and be released. That’s where Dan Clayton (6223), a chemical engineer at Sandia, and his team come in.
Working for DOE, they are assessing the potential risk of possible accidents for the Mars 2020 mission. Using state-of-the-art computer programs, they test what would happen to the RTG if the rocket were to explode on the ground or in mid-air.
Rugged protection put to the test
RTGs are designed to minimize any possible release of radioactivity. Modern RTGs use plutonium-238 in an insoluble, ceramic form. Each pellet of plutonium is encased in a strong, non-reactive metal — iridium. These metal-wrapped pellets are then encased in layers of carbon fiber to protect them from physical impacts and the heat of launch area fires or reentry.
Dan’s team puts the rugged, multi-layer containment system to the test by running mechanistic-based computer models on advanced supercomputers, validated with experimental data.
“We try to validate every aspect of our models with the data we have. But it’s hard to convince anyone to blow up a rocket,” says Dan. Even without blowing up an actual rocket costing upwards of $100 million, the team has access to large amounts of data from smaller-scale tests.
Data from solid propellant fire tests conducted at Sandia’s Thermal Test Complex and the Johns Hopkins University Applied Physics Laboratory (APL) are used to validate the computer models of extreme heat from burning rocket fuel.
The results from impact tests at Los Alamos National Laboratory (LANL) and early tests at Sandia’s Rocket Sled Track are compared to the damage the models predicted from the rocket plummeting to the ground.
The durability and ductility of the iridium metal that encases the plutonium is tested at Oak Ridge National Laboratory (ORNL) and Sandia’s Engineering Science Center.
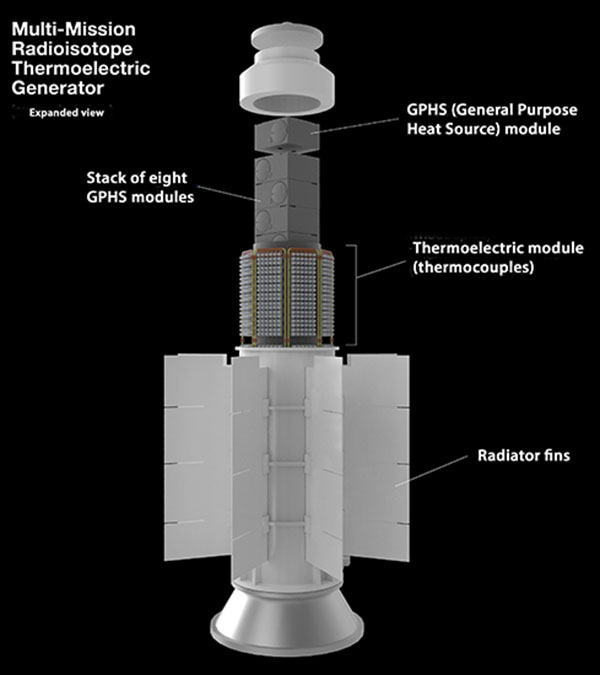
Labeled pull-apart view showing the major components of the Multi-Mission Radioisotope Thermoelectric Generator. (Image credit: NASA)
Even data from accidents are put to good use
But not all of the data Dan’s team uses come from experiments. “We don’t plan on getting accident data, but when an accident happens, we use that to validate our damage models too,” says Dan.
For example, in 2014 an International Space Station-bound rocket exploded just seconds after liftoff at NASA’s Wallops Flight Facility. In the days after — while others were involved in mitigating the environmental impact and determining the cause of the accident — Dan and his team headed to launch site at Chincoteague Island, Virginia. They analyzed the damage and compared it to what they calculated for a similar event. Specifically, they validated their fireball models and their smoke plume models. None of the data from the accident invalidated previous safety analyses, says Dan, and it reduced the overall uncertainty of their models.
Luckily the 2014 rocket accident didn’t result in any injuries and didn’t contain any nuclear material.
“Accident rates in this industry are relatively high — 2 to 3 percent — which is why this work is so important,” says Ken Sorenson (6223), manager of Sandia’s risk assessment team. “We’re not guaranteeing that there cannot be a radiological consequence as a result of a potential launch accident. What we do is estimate potential radiological consequences from postulated accidents. Then it’s up to the decision makers to determine if that level of risk is acceptable.”
Dan’s team has just begun the multiyear process of assessing the risks of various possible accidents for the Mars 2020 mission. “The results of the assessment are used to identify the main sources of risk, allowing us to reduce the overall risk of the mission before launch,” says Dan.
The safety assessment will be reviewed by the Environmental Protection Agency, Department of Defense, NASA, and many others. Eventually the assessment will be submitted to the Office of the President for launch approval.
Technical experts across Sandia will collaborate on the risk assessment with LANL; ORNL; APL; NASA’s Jet Propulsion Laboratory and Kennedy Space Center; and the University of Dayton Research Institute.
Ken says, “The breadth of science required for this risk assessment is really well-suited to Sandia’s toolbox because we have technical experts in experimental fields and we have technical experts in running and developing codes. This capability set, coupled with world-class experts from organizations across the US, brings together a team that really allows us to address this problem from beginning to end.”