Composite materials testing part of Sandia’s national security mission
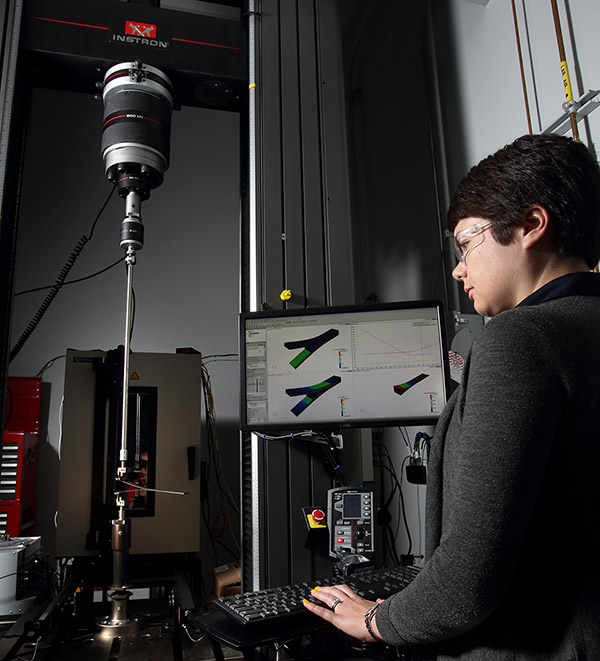
ADVANCED STRUCTURAL TESTING – Stacy Nelson (8259) works on improving the understanding of how composite materials behave when they are subjected to the different types of loading environments. (Photo by Dino Vournas)
Sandia scientists and engineers are developing computer simulation tools capable of making realistic and reliable predictions on the performance of composite materials and structures.
“Sandia is interested in composite materials as part of its national security mission,” says stress analyst Stacy Nelson (8259). “We need to improve our understanding of how the composites behave when they are subjected to different types of loading environments.”
Currently, Sandia is conducting research on the fracture and failure of advanced materials, specifically fiber-reinforced composite materials and their response to different loading environments, which can include mechanical shocks and vibrations as well as large temperature variations.
“Composites are of interest to Sandia for a number of structural applications,” Stacy says. “To optimize composite design, we need state-of-the-art computer simulation tools to make predictions regarding the behavior of a composite structure and know that they’re accurate.”
Stacy and her computational team collaborate with experimentalists in other Sandia departments. Experiments can occur while models are running, allowing immediate comparisons to ensure the work is on the right track.
The team has published several papers and the research has been well-received at conferences. The team includes Stacy, Shawn English (8248), Alex Hanson (8259), Timothy Briggs (8222), and Brian Werner (8343).
Arthur Brown, manager of Multi-Physics Modeling and Simulation Dept. 8259, says the team does an excellent job of improving the modeling tools, using uncertainty quantification and validation methods to improve model credibility, and working directly with customers to provide the design support they need.
“The team of modelers and experimentalists has formed a well-integrated effort, even setting up external collaborations with researchers at the Air Force Research Laboratory,” Arthur says.
Composite materials 101
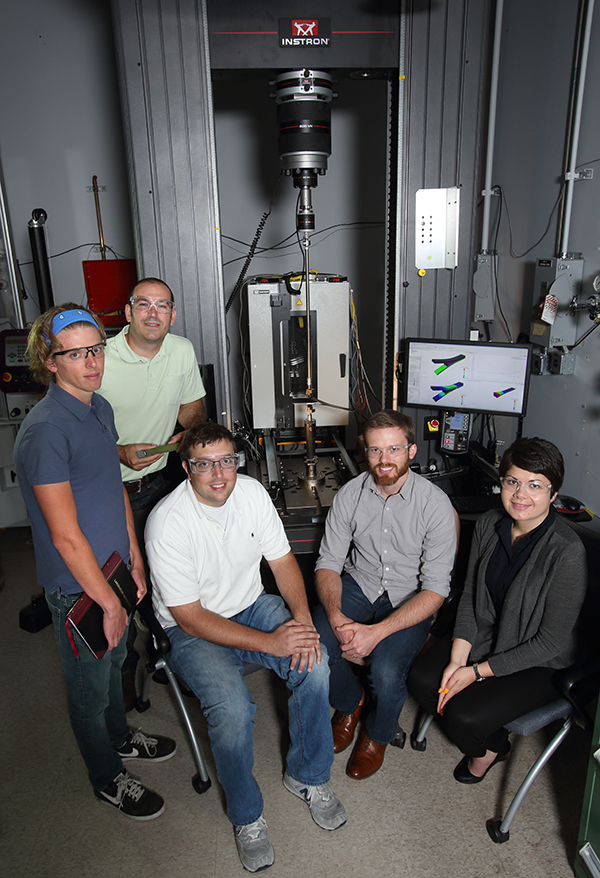
COMPOSITE COLLABORATERS — Sandia scientists and engineers continue to collaborate on fracture, failure of advanced structural materials. They include, from left, Alex Hanson (8259), Tim Briggs (8222), Brian Werner (8343), Shawn English (8248), and Stacy Nelson (8259). (Photo by Dino Vournas)
Composite materials are made from two or more materials. An example is a fiber-reinforced composite, in which strong, stiff fibers are embedded in a matrix material. In general, since the fibers are strong and stiff, they are the load-carrying members of the composite, while the matrix materials keep the fibers properly oriented and protected from the environment. The blending of different fibers with matrix materials can produce a combination of properties that can be tailored to a specific loading environment, ensuring that the composite is strong enough to withstand any intended weights or pressures.
In addition to their use in Sandia’s national security mission, composite materials are also used in lightweight vehicles, racecars, and wind turbine blades.
Composites have many advantages, including superior strength-to-weight and stiffness-to-weight ratios. But designing with composites can be difficult.
“Composites are of interest both academically and for actual applications,” Stacy says. “The challenges associated with modeling them aren’t new.”
Surprising effects of residual stress
To design and move forward with composite structures, the Sandia team is validating and verifying analysis tools to ensure computer predictions and their expected behaviors are accurate.
The team is currently using a building-block methodology in which materials experiencing fracture are isolated and examined individually prior to investigating more complex combinations of fracture-related behaviors. Researchers study the interaction of a composite material’s makeup at the microscale.
“We start at small scale and look at each individual phenomenon and then expand from there,” she says. “This provides material properties that we can use in simulations of a macroscale. Then we try to look at interlaminar delamination, or the debonding of adjacent layers in a composite and at the effects of fabrication-induced residual stresses.”
Moving forward, researchers combine the two phenomena to create a larger, more realistic structure.
Stacy says residual stress is one of the most interesting aspects of the current research. “If fiberglass and carbon fiber are bonded together, residual stresses will form in the structure because carbon fiber and fiberglass expand and contract differently during the thermal cycles,” she adds.
“We’ve observed that these residual stresses increase the load at which the composite will delaminate, meaning the composite can actually bear more weight. Intuitively one would think that these residual stresses that live in the composite from the very beginning would perhaps lower its load-bearing capacity. But it looks like it is increasing. This is very promising, since these residual stresses could potentially be taken advantage of and incorporated into structures to increase their performance.”
As the computational methods under development continue to be numerically verified and experimentally validated, these analysis techniques can be implemented with increasing confidence to support various aspects of Sandia’s national security mission, says Stacy.