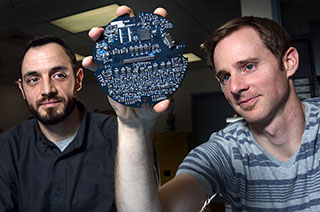
WEAPON PERFORMANCE DATA COLLECTORS — Brett Chavez and Jerrod Peterson (both 8135) build and test high-performance instrumentation systems for ground and flight tests. (Photo by Dino Vournas)
As Sandia’s nuclear weapons program continues to execute three full-scale engineering development programs to help extend the life of the stockpile, Sandia’s Telemetry Systems departments have seen a dramatic increase in their work in designing, building, and testing high-performance instrumentation systems for ground and flight tests.
These organizations are responsible for developing data instrumentation systems to support various nuclear weapons programs for the DoD and NNSA.
The systems created at Sandia/California are used by weapon development and stockpile evaluation programs to collect weapon performance data, which is used in qualification activities and annual assessments.
The next generation of telemetry systems
Since the early 1980s, Sandia/California has helped lead the telemetry systems work for the Joint Test Assembly (JTA) program for the nuclear security enterprise. Currently, the California groups are working on several new telemetry systems to support the W88 ALT 370, B61-12, W80-4, and Mk21 fuze program.
In addition to the high number of simultaneous development programs being supported, the amount of hardware being requested by these programs is at an all-time high. The telemetry groups do a large majority of this hardware development before transitioning it to the National Security Campus in Kansas City, Missouri. In today’s environment of high-rigor qualification activities, the amount of hardware needed over the life of the program development to support their system-level test units has increased from a few handfuls in the past to today’s steady stream of test units for the W88 ALT370 and B61-12.
Fully prototyped and proven operational
These newest telemetry (TM) designs also include new features. For example, earlier this year, the B61-12 telemetry team added a data recording capability to its instrumentation system design. The team’s goal was to ensure all contact fuzing end-event data will be captured during surveillance flight tests.
“This recorder — christened the HDR (hardened data recorder) — must be capable of recording all critical weapon-scoring data in milliseconds while surviving free-fall ground impacts,” says Ryan Layton (8133). “A team of engineers from 8133 took on the challenge of building a smaller version of the HDR, leveraging the experience they gained building the B61 JTA modernization flight recorder.”
“The HDR is a small part of the B61-12 JTA telemetry system that plays a big role,” says Tim Kostka (8133). “Its job is to record and store data critical to assessing the reliability of the weapon.”
This is achieved by containing the electronics in a stainless steel housing and encapsulating them using dense, rigid foam. As part of the design process, the HDR will go through rigorous testing, including shock testing, before it is delivered and flown in the system.
The HDR has already been fully prototyped and proven operational during benchtop testing. From mid-August through September the product will undergo physical and thermal testing for performance at high temperatures, extreme cold temperatures, and a range of other environmental and mechanical conditions.
Development of new capabilities and technologies
Another challenge for these groups is finding ways to provide more and more data while still living within system-level design constraints.
The W88 ALT370 team recently successfully delivered units for an Environmental Development JTA (EDJTA). The purpose of the EDJTA flight bodies was to gather data as seen by the weapon throughout a typical flight profile. This information will be used to help create and validate environmental requirements for Weapon Reserve components. These units captured multiple channels of data from sensors located throughout the flight test body.
To be able to monitor the multiple channels of data at the requested sampling rate and transmission bandwidth needed by the W88 systems organization, the TM engineers needed to come up with a more efficient way of collecting and transmitting data.
They did this with two new design features. One was the implementation of a new compression algorithm, which allowed three times as many sensors to be monitored as would have been possible without compression.
“The algorithm allows transmission of the same or similar information in fewer numbers of bits,” says Bruce Brunett (8943). “In telemetry systems the goal is to balance between the amount of information conveyed and the bandwidth used in the transmission.”
There is a constant push to get more data from the units. But the limiting factor is the receiving assets on the ground that constrain the amount of information that is sent. The main objective was figuring out a way to get more information with fewer bits.
“The system was pretty challenging to implement,” says Jerrod Peterson (8135). “The work was driven by a real application, customer request, and also based on goals for the program. The challenge was placed on the team and we made leaps in capabilities.”
The compression algorithm is also currently being used by other program telemetry teams as well.
The second enabling feature in the W88 EDJTA bodies was the incorporation of a new transmitter that uses RF bandwidth more efficiently than the pulse code modulation — PCM — used in previous transmitter designs. Use of this modulation method allows a substantially greater percentage of data to be transmitted within the same RF bandwidth allocations.
A new battery pack
The W88 ALT TM also uses a new battery pack designed and developed by Sandia in Albuquerque. The new battery allows the TM to record environmental data prior to launch while the unit is still with the launch vehicle. This is a first for JTAs.
Typically a chemical battery is activated after launch and there is no way to collect in-tube data. Getting enough capacity in a small volume and getting certification for the battery to be flown during the test were two hurdles the group had to overcome. The battery went through extreme testing until approved for usage.
The telemetry groups work closely with organizations throughout the Laboratories and rely on them to meet delivery of the products
“Our work touches so many organizations including design engineering, shipping and receiving, test facilities, epoxy lab, and materials lab,” says Kathryn Hughes (8133). “All those people have done a wonderful job in supporting the telemetry systems groups in meeting its mission.”
Jennifer Clark (8135) adds, “We would not be able to fulfill our mission without them and because of these interdependencies, our engineers get to learn about the wide variety of capabilities and support that the laboratory has.”
The TM groups also interact with every weapon system since every system utilizes a TM system developed by these organizations. This gives these engineers a strong insight into the systems designs. “This makes TM a good stepping-stone for designers wanting to eventually to move into systems work,” says Jennifer.
In addition to this internal collaboration, the TM organizations work closely with partners at other DOE sites.
The future
There doesn’t appear to be any downturn in work for the telemetry groups any time soon. Within the next few years, as the current programs ramp down the W80-4 will be ramping up and several weapon systems groups are planning JTA refreshes.
In addition to this, the teams would like to invest in some new R&D activities including improved detonation monitoring and various kinds of optical sensing.
“We have a bright future,” says Jennifer. “We get to design, build, test, and deliver lots of hardware which not everyone here onsite gets to do and we learn from each iteration. It’s an exciting and challenging environment for our engineers.”