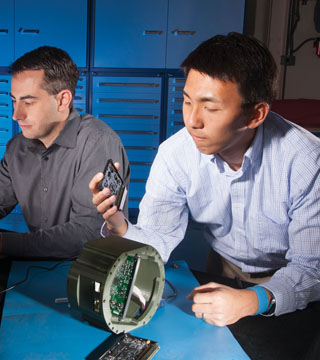
Stephen Downey (8135) and former Sandian TaiWen Ko evaluate adaptable telemetry hardware components as they build up the telemetry system to be used to test the Mark 21 replacement fuze. TaiWen is inspecting an environmental sensor measurement card of the telemetry system while Stephen modifies the firmware to be loaded onto the card’s field programmable gate array. Stephen and TaiWen are adjusting the hardware and firmware capability to increase bandwidth and hence provide more measurement capability of the W87 fuze and its environments during test flights. (Photo by Randy Wong)
If the term “fuze” seems more prevalent around Sandia these days, it’s no accident. Technical staff and managers, systems engineers, flight test specialists, and project managers across the Labs are actively engaged in the Mark (Mk) 21 Fuze Replacement program for the W87 warhead on the US Air Force Minuteman III intercontinental ballistic missile (ICBM), an engineering development effort that promises to remain a key activity for Sandia’s nuclear weapons mission for years to come.
Mounted at the forward end of the warhead, the fuze tracks the path of the warhead and gives the signal to detonate. To fulfill this role, many intricate components must operate perfectly in challenging environments, which in turn calls for very careful engineering. Sandia has been providing such engineering for decades for the arming, fuzing, and firing (AF&F) sets of several US Navy submarine-launched ballistic missile warheads.
The Mk21 Fuze program — led by Dept. 8242 in California and drawing on extensive engineering from New Mexico teams in Divisions 2000 and 5000 — leverages and consolidates Sandia’s proficiency. “Sandia has provided fuzing systems for the Navy for more than 40 years,” says Curt Nilsen (8242), manager of the ICBM Fuze Systems Engineering Group. “We’re now proud to bring our expertise to the Air Force.”
Optimizing commonalities
Sandia’s long-standing and productive working relationship with the Navy was a strong factor in the Air Force selection of Sandia to design the replacement Mk21 fuzes. Contracting with Sandia also created the opportunity to gain efficiencies by leveraging commonalities between the Air Force and Navy fuzes through the W88 ALT 370 program.
“The two fuzes themselves won’t be identical, but several of the key components will be the same,” Curt says. “Other parts will use similar technologies, but will be modified to meet unique Air Force needs. Both the Navy and the Air Force have been actively supporting efforts to optimize this integration,” he adds.
Sandia started work on the project in November 2011 with the goal of creating the first production units in the early 2020s. Production is expected to continue through 2029.
The Sandia teams have been busy refining product requirements, creating and prototyping their designs, and planning for qualification. Still to come is more detailed component design that will further specify the form and function of elements — and show how these specifications allow the elements to meet all requirements. Qualification activities will demonstrate component and system performance and robustness and will include a series of system-level ground and flight tests.
Top-of-the-line program management
In embarking on the Mk21 project, Sandia and the Air Force recognized the challenges created by a decision to apply the NNSA Phase 6.X NW development process, rather than the Defense Acquisition Process (known as the DoD 5000 process) historically used by the Air Force.
“Both processes are thorough, but it isn’t possible to map every step in one process to a step in the other,” says Curt. “So to gain the customer’s confidence that Phase 6.X would fulfill the letter and spirit of DoD 5000 and ensure that all project requirements would be met, we knew top-of-the-line project management processes would be required.”
As a first step, project leaders built a team of technical project managers that included several hires with extensive DoD 5000 experience. Because of customer needs, leaders also decided to implement an earned-value management (EVM) system — a highly structured way to assess work completed and budget spent against a plan. They then fostered an environment that enabled the project managers to work as peers with their R&D counterparts in implementing EVM.
Curt says that EVM increases the rigor of project management and offers the team an accurate picture of the status of the project and progress against plans and budgets.
Coordination is key
The project relies heavily on teams from across all of Sandia. In broad strokes, Dept. 2135, led by Ron Franco, is responsible for engineering the fuze hardware, while Dept. 8242 is taking the lead on systems engineering, flight tests, and project management. All these activities must take place in tandem and drive toward the common goal of ensuring that the fuze meets all of its customer requirements, on time, and within budget.
Curt says the need for close coordination has required an extra emphasis on communications between the two sites, a message seconded by Ron. “This project is exceptional in bringing people together across the sites and ensuring that we are aware of the work of other teams and actively contributing across sites as needed,” he says.
Other key California organizations working on the project include W87 Systems Engineering (8231) and Telemetry and Stockpile Support (8135). Fuze component development is provided by Nuclear Weapon Arming & Fuzing Systems (5350), Firing & Embedded Systems (2620), Advanced Mechanical Design (2610), and Power Sources & Metrology (2540). Centers 1700, 1500, 1300, and 1800 also play important roles.
Maintaining a cutting-edge NW workforce
Besides extending Sandia’s fuze expertise to a new system, the Mk21 program is significant because it is one of three Sandia programs — along with the B61-12 Life Extension Program (LEP) and W88 Alteration (ALT) 370 effort — that are in “Phase 6.3” or full-scale engineering development.
Sandia activity in weapons modernization has not been this high since the early 1990s, a fact highlighted by Labs Director Paul Hommert in his testimony to the US House Armed Services Subcommittee on Strategic Forces, provided in October 2013.
Cutting-edge projects such as the Mk21 Fuze Replacement Program keep Sandia employees at the forefront of a wide range of technology advances, from electronics to environmental testing. The fuze project also gives employees opportunities to develop and work with hardware — work that many find deeply satisfying.
In testifying to the House subcommittee, Paul noted that 500 of Sandia’s new hires, many in the early stages of their careers, are working on new weapon projects. Said Paul: “The modernization program provides opportunities for these new technical staff to work closely with our experienced designers: from advanced concept development to component design and qualification, and ultimately to the production and fielding of nuclear weapon systems.”
In turn, this provides new technical staff with “the multiyear learning it takes to technically steward the nation’s nuclear stockpile now and into the future, after the modernized warheads are in the stockpile.”
Put simply, programs such as these are critical to building the skilled technical workforce Sandia needs to execute its mission and ensure an effective nuclear deterrent for decades to come.