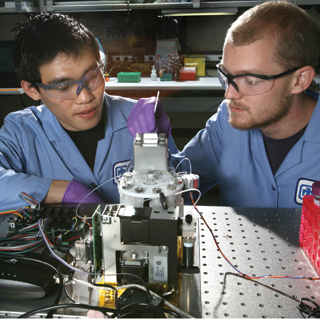
On popular television shows like CSI, it often seems that detectives send DNA crime scene evidence to the forensic lab and have their results in hand after a single commercial break.
“In real life, an entire laboratory filled with technicians and PhD-level scientists using equipment worth thousands and even millions of dollars is at work analyzing those samples, a process that can take hours if not days,” says Michael Bartsch (8125). “That fade-to-commercial glosses over a lot of time, effort, and expertise.
Mike is leading a project for the US Army Criminal Investigation Laboratory (USACIL) that aims to make the practical process of forensic DNA analysis more closely match the duration of that commercial break, at least in part. Over the last year, Mike and the science and engineering team in Advanced Systems Engineering & Deployment Dept. 8125 have been developing a prototype Battlefield Automated DNA Analysis Sampling System, an instrument designed to enable rapid DNA fingerprinting (genotyping) in a field-portable package.
Currently, DNA samples collected in Afghanistan, for example, may be sent to a containerized laboratory at a US or Coalition base in-theater, or to the USACIL headquarters outside Atlanta for forensic analysis. The Battlefield DNA Analysis System will ultimately help bring that laboratory capability to investigation sites near the front lines and provide results in about an hour.
“It takes time to transport a sample back to the lab,” says Ken Patel (8125). “The forward-deployed forensics labs reduce the travel time, but still require highly trained scientists and specialized equipment. The Army has a real interest in rapidly processing DNA samples to aid decision-making for emerging military and intelligence needs” And, as in the case of confirming the identity of Osama Bin Laden, the turnaround time required for DNA analysis can be critical.
In particular, the Army wants to use rapid DNA analysis in investigations of improvised explosive devices (IEDs) to identify bomb-makers and their associates. Even after an explosion, investigators can often collect usable DNA from IED remnants. Other potential applications include screening at checkpoints and detention centers or determining which individuals may have been present at places of interest, such as terrorist training camps.
The Battlefield DNA System brings together four traditional benchtop DNA sample preparation steps: extraction, quantification, amplification, and separation. Amplification, or polymerase chain reaction (PCR), is critical for touch and trace DNA samples like those collected from IED components.
“You can start with a very small amount of DNA, even just one copy, and amplify it until you have thousands of copies that you can readily measure,” says Mike. “It’s a very powerful technique that makes it possible to obtain DNA analysis from an actual fingerprint. It’s also very challenging to implement outside a laboratory environment.”
Digital Microfluidic Hub
Key to bringing together these four steps in an automated, portable platform is the Sandia Digital Microfluidic Hub, a tool for manipulating and transporting microliter-scale sample droplets using electrostatic forces. Initially developed for the RapTOR (Rapid Threat Organism Recognition) Grand Challenge, this technology won an R&D 100 Award this year (Lab News, June 29, 2012) and last year garnered the Society for Laboratory Automation and Screening’s innovation award (Lab News, April 22, 2011).
The Hub acts like a network router, directing, assembling, translating, and scheduling the movement of discrete packets — in this case DNA and reagent droplets — to and from the four sample processing modules.
“The Microfluidic Hub allows us to optimize each of those modules independently. They don’t need to be compatible with each other, only with the Hub,” says Ken. “It really streamlines what would otherwise be an almost intractable engineering problem.”
This difficult, multidisciplinary problem requires a diverse and well-integrated project team.
“Engineering team lead Ron Renzi [8125] contributes a strong mechanical design and systems engineering ethic. Electrical engineer Jim Van DeVreudge [8125] has the expertise to seamlessly interface hardware controls with the software developed by our programmer, Dan Knight [independent contractor]. And Mark Claudnic’s [8233-1] CAD designs and assemblies are brought to life by Jerry Inman [8125], an expert technologist in electronic and microfluidic systems,” Ken says.
With a couple months remaining on the project, the team has built and tested prototype hardware for most elements of the DNA analysis platform. Summer interns are currently testing an automated DNA extraction module that uses a commercially available protocol for isolating DNA from cheek swab samples, but adapts it to work without a benchtop centrifuge or other bulky laboratory equipment — all in a footprint smaller than a shoebox.
The PCR amplification component also is nearing completion. This module uses a novel rapid thermal cycling approach for which the team has filed a technical advance and hopes to submit a patent application. “We’ve got the testbed PCR prototype integrated to a level where you introduce the sample, push a button, and walk away. Ninety minutes later, you have a result,” says Mike.
Even the separation module, a fairly typical capillary electrophoresis design, uses unconventional components to enhance capability. In this case, a low-cost spectrometer the size of two decks of playing cards allows the system to work with virtually any commercially available DNA fingerprinting kit without the need to reconfigure system optics or include multiple kit-specific filter sets.
In the next few months, the modules will be connected through the Microfluidic Hub and the proof of concept prototype will be delivered to USACIL. “It will be a benchtop-integrated prototype that they can test and give us feedback,” says Mike. “Moving forward, we will optimize for size, speed, and performance.”
Forensics is not a traditional area of research for Sandia, but Ken expects that to change. “It plays well to our strengths in microfluidics, bioassays, and system integration,” he says. “This opportunity could open new areas of business for Sandia in developing sample preparation platforms for field and laboratory use. The FBI, for example, may not need portable analysis, but they have huge casework backlogs that could make the speed of our system very attractive.”