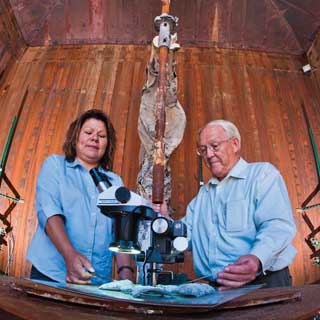
FIERY STUDIES – Sylvia Gomez-Vasquez and Walt Gill (both 1532), in the burn chamber in Coyote Canyon, demonstrate the early stages of sample analysis of crusty pieces of burned debris such as might occur after a rocket propellant fire. Sandia signed a three-year contract with the Jet Propulsion Laboratory (JPL), California Institute of Technology, with funding from NASA, for a propellant fire modeling project. (Photo by Randy Montoya)
Walt Gill of Sandia’s Fire & Aerosol Sciences Dept. 1532 calls it a pancake – a disk more than a foot in diameter covered with what looks like the debris you’d scrape off a particularly messy barbecue grill. It’s actually a crunchy, baked-on mixture of aluminum, aluminum oxide, carbon, and other chemicals that coats everything after a rocket propellant fire.
The gritty material is part of a study Sandia is doing under a three-year contract signed with the Jet Propulsion Laboratory (JPL), California Institute of Technology, with funding from NASA. The propellant fire modeling project began in February and expands beyond the risk analyses the Labs already does for DOE. A presidential directive requires DOE to assess the risk to the public of launching NASA space missions that carry radioactive material for power sources. It contracts with Sandia for those assessments.
A propellant fire is one of the major risks in launching space missions with radioactive material, says Ron Lipinski (6223), team leader for the risk analysis. Consider, for example, if fiery fragments from a launch accident landed on top of nuclear batteries and burned at a temperature high enough to melt one of the containment boundaries.
Ron’s team needs information to assess overall risks, and this year JPL teamed with Sandia’s fire sciences group to provide technical information on propellant fires for what’s called the databook, a report on potential accidents that could occur during launch. JPL is managing the activity.
Advanced modeling is key
Walt says the key to Sandia’s contribution is advanced computer modeling focusing on characteristics of propellant fires.
“It would be a combination of experimental data and model results that would work together to give them the information they need,” he says.
The databook becomes the foundation for assessing risk. “Sandia is able to use our broad range of expertise, from experiments with various environments to modeling to our risk analysis process and safety analysis,” Ron says.
The work builds on tools the Labs created in nuclear weapons programs, including data from propellant fires it has studied since the 1970s, Walt says. “What Sandia has contributed that’s original into this whole mix is the idea of putting test data together with multi-physics high-fidelity models and looking at them as one piece,” he says.
Coupling experimental data with high-fidelity modeling in the databook hasn’t been tried before, so researchers in Advanced Nuclear Fuel Cycle Technologies Dept. 6223 are building an interface between
Sandia’s physics-based computational model of a fire environment and DOE’s radiological response model.
The interface is one of three parts to the project. The team also will update the computer model and add features to predict how things will behave in a propellant fire, then develop experimental data to validate the model. Tests will be done in the contract’s final year.
“That’s what sets Sandia apart,” Walt says. “We model, predict, experiment, compare. The Sandia way is we make the model first. … It’s like the scientific method; you come up with a hypothesis and test it.”
At a very basic level, Anay Luketa (1532) likens modeling and simulation to a high school algebra function with a value in and a value out. “From an engineering perspective, modeling requires the development of equations that approximate physical processes we’re interested in. Once developed, they are put into computations where the inputs are in the form of geometry, material characteristics, boundary conditions, and initial conditions, and the outputs are such quantities as temperature and velocity.”
The complexity of this particular problem is increased by the makeup of rocket propellant, which has an oxidizer, a rubber binder, and aluminum powder for fuel. Under conditions representative of a launch accident, aluminum powder burns slowly, melts on the surface of the propellant, and is lofted up into the flame, where it burns like droplets and leaves gritty deposits on everything, Walt explains.
The risk assessment is interested in the chemical makeup of the deposit and the temperature in its layers, says Walt, hefting a large clear plastic bag of ashy-looking chunks. “This stuff comes from the aluminum that is burning in the flame. It hits the surface, goes out. It becomes really thick.”
Sandia is improving its overall model by focusing on models for the droplets and the coating’s chemical makeup.
Walt unrolls a poster showing a microscopic analysis of a 2 cm slice of the material. He points out different parts of what looks like a cross-section of a rock: “The white is aluminum. Gray is aluminum oxide and lighter gray is hydrochloric acid and more aluminum. The dark spots are empty space.”
Burl Donaldson, a New Mexico State University professor who worked at the Labs for a dozen years, studied what aluminum does in an atmospheric burn when he was at Sandia in the mid-70s.
Comparing Rocstar and Fuego
“We have the same problem 35 years later,” says Burl, a part-time researcher on the team. “I don’t think anyone represents that we will put this issue to rest, but we hope to learn more about it.”
Anay says it’s one thing to study a single aluminum droplet – there are numerous technical papers on that – but it’s another to study it in the complex physics of a propellant fire.
“It’s very hard in a real propellant environment to capture the true dynamic behavior experimentally,” she says.
She’s been studying a code called Rocstar, developed by the University of Illinois under a DOE-funded Advanced Simulation & Computing program. It’s designed to run massively parallel and has been tested through a rigorous verification and validation process similar to what Sandia applies to its codes. She’ll spend much of the summer seeing if Rocstar will meet the project’s needs. Sandia also has its own fire modeling code – called Fuego, Spanish for fire.
Walt says the team wants to run both programs and compare them.
The team also can leverage ongoing work on weapons systems involving melting and burning aluminum to study how materials respond, he says. Anay says much of the outside data on aluminum doesn’t deal with high temperatures or fire environments.
Bill Erikson (1516) says the model has to capture convection, or the flow of hot gases over a surface; thermal radiation transfer; and the thermal loading associated with the accumulating grit with its varying particle sizes and distribution.
Burning aluminum particles are extremely hot, reaching about 4,940 degrees Fahrenheit or more, Bill says. As they radiate out, countless tiny, very hot particles slam into surfaces, leaving the gritty chemical buildup.
Integral validation
Sandia researchers have designed models for the heat transfer occurring with the deposition, and they’ve added changeable properties to account for growing deposit layers, Bill says. Still, he says, the models don’t yet capture such things as chemical reactions where molten aluminum hits other surfaces.
Eventually, the team’s work will be added to large codes. “It’s one thing to understand; it’s another thing to make them predict something,” Walt says. “This is the result of a lot of work by a lot of people to give us these big machines and these big models.”
The team also will do integral validation – validating a model by putting all the pieces together, such as through an accident scenario.
“You do the calculation, predict what it’s going to do, and then you do the experiment and see if that’s what happened. You put everything in there, not just one part,” Walt says. “So these experiments can get large and complex. It might take six months to set up and a minute to do it.”