On May 19, student winners of the fifth annual Sandia-sponsored MEMS University Alliance Design Competition, aided by their professors, presented their visions of astonishingly tiny yet productive machines to the scrutiny of Sandia’s seasoned microelectromechanical systems group — arguably one of the most advanced MEMS design and fabrication groups in the world.
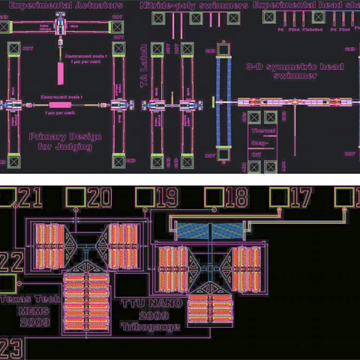
The 2009 winner in the “novel device” category was a “microswimmer,” which resembles a tiny fish and is designed to swim like one, its aluminum tail whipping back and forth as it is heated and cooled by periodic bursts of microwave radiation. The design was created by Kevin Bagnall of the University of Oklahoma’s School of Aerospace and Mechanical Engineering, and presented by graduate student Jeff Lantz under the direction of professor Harold Stalford.
Fantastic Voyage
“Think Fantastic Voyage,” says Sandia senior microfabrication manager Tom Zipperian (1740), referencing, as a possible future use for the design, the movie that portrayed a vessel shrunken enough to navigate the human body by touring its bloodstream.
A second area of competition — a device to characterize and test the reliability of tiny devices — was won by a design that Texas Tech University students termed a “tribogauge,” used to determine the wear, friction, stiction, and lubrication of moving parts of MEMS devices, on-chip and in situ. (These determinations are called tribological.) The work was presented by student Ganapathy Sivakumar under the direction of associate professor Tim Dallas.
Also participating in this year’s contest were the University of Illinois at Urbana-Champaign, the University of Utah, and the Air Force Institute of Technology.
“This year’s group was again very competitive,” says design contest leader and MEMS Core Technologies team lead Mark Platzbecker (1749). “Each year, the designs get better and the associated white papers more professional.”
Among universities now going through the process to join the alliance but not yet signed up are Cornell and the University of New Mexico. Duke University and the Rose-Hulman Institute of Technology in Terre Haute, Ind., have also expressed interest. More than 20 educational institutions are members of the alliance.
The contest, which took place in a conference room at Sandia’s MESA center, is intended to take students beyond the academic classroom into a world where MEMS devices are of high significance — “a career-altering moment for some student engineers,” says Mark.
The University of Utah’s MEMS team leader and professor Ian Harvey agrees. “I can bleed all over the paper in a classroom,” he says, “but that’s different from being here.” He gestures at the Sandia MEMS personnel and the imposing conference room, with its 30-foot-high ceiling, reserved for the team presentations. “I’m dealing with engineers early in their careers. This can make them passionate about their work.”
Increased interest
From Sandia’s point of view, says Tom, the contest brings in new design ideas, provides impetus to universities to train the next generation of MEMS engineers, permits Sandia engineers the satisfaction of acting as mentors, and allows Sandia to partner on university grants from the National Science Foundation that are ordinarily closed to the national labs.
The program has drawn increased interest from universities, says Mark, perhaps because the latest flat-screen digital light processing — DLP — TVs use MEMS mirrors to switch pixel colors, and MEMS accelerometers provide key sensing elements in popular Wii game controllers.
Still, from a university’s point of view in a time of cutbacks, says Harvey, “MEMS is called a boutique course. Administrators ask, ‘Why don’t we just teach the basics? Cover fundamentals? Train people who can find jobs?’”
Harvey says his problem with that outlook is that “a lot of kids are vacillating. They’re not sure what they want to do. Instead of throwing them into a thermodynamics class, we offer a nontraditional class. There are no books or tests. Instead, there’s design, simulations, continuous feedback, and talk about reliability and packaging.”
“It’s the machine shop of the future,” says Tom, “and, here at Sandia, at the most advanced MEMS facility in the world, we have the personnel to help alliance members through problems. But a university has to make a significant investment in tools and education to get its program going.”
The alliance helps by providing classroom teaching materials and licenses for Sandia’s design tools at a very reasonable cost. This makes it possible for a university without its own fabrication facilities to develop a curriculum in MEMS.
No instant gratification here
Contest participation is the opposite of instant gratification. The entire process takes almost nine months. It starts with students developing ideas for a device, followed by creation of an accurate computer model of a design that might work, analysis of the design, and finally, design submission. Sandia’s MEMS experts and university professors review the design and determine the winners.
Sandia’s MESA fabrication facility then creates parts for each of the entrants. Once the parts are fabricated, they’re shipped back to the university students for lengthy tests to determine whether the final product matches the purpose of the original computer simulation.
Among factors of continual interest to MEMS fabricators and designers are friction, stiction, temperature, humidity, and surface topography.
The university alliance coordinates with the Sandia-led National Institute for Nano Engineering (NINE), providing additional opportunities for students to self-direct their engineering education, and the Sandia/Los Alamos Center for Integrated Nanotechnologies (CINT), a DOE Office of Science center with the most up-to-date nano-technology tools.
The winning MEMS design contest entries
The University of Oklahoma’s microswimmer is the first known microscale artificial swimmer capable of being produced in batches of 100 by the process known as surface micromachining — the most widespread technique used worldwide to fabricate micromachines, and in which Sandia’s facility is a leader. The swimmer’s free-swinging tail is 40 micrometers in length. The different rates of expansion and contraction of a tail strip with one side aluminum, the other polysilicon, when heated by a cyclically powered microwave, set the tail wagging, propelling the swimmer forward at an average speed of 3.3 micrometers/second. Potential applications include research and drug delivery in the body.
The tribogauge design uses comb drives — interlaid sets of “teeth” that, when electrically charged, attract each other. These normally are used to drive rods that power microgears or latches. Texas Tech student designers propose using this device not only for power but, treating their parallel comb teeth like capacitors, as sensing devices. With this and with pads that extend off the surface of the chip, the gauge will detect wear, friction, stiction (the force needed to break an object out of its stationary position), and lubrication of various MEMS devices in situ, including those actuated by electrostatic and electrothermal means.