Taking a look at TRUPACT-III with David Miller, manager of Sandia’s Materials Transportation Testing and Analysis Dept. 6765, the first adjective that comes to mind is “big.” The massive transportation container is impressive by any standard. TRUPACT-III is designed specifically to move large items to the Waste Isolation Pilot Plant site near Carlsbad, N.M., David says. The 8.2- by 8.7- by 14-foot stainless-steel, 55,000-pound package is designed with multiple layers to protect its cargo.
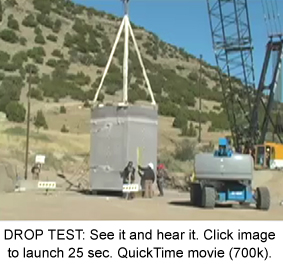
Walking around TRUPACT-III, David points out the protected heads of giant bolts that hold its heavy, stainless-steel lid protection panel in place. (The actual lid is buried two feet into the package.) The energy-absorbing foam between inner and outer container boxes can’t be seen, but its presence is acknowledged by blowout plugs in the outer package. These plugs allow the foam to expand and escape in case it is caught in a fire, he says.
During the past two weeks, a team of Sandia researchers in remote Coyote Canyon have been testing the mettle of TRUPACT-III for its builder, Packaging Technology, Inc. (a subsidiary of Areva), to determine if it can qualify for Nuclear Regulatory Commission certification. A Sandia team has chilled the giant container to minus 40 degrees F, dropped it 30 feet onto an unyielding surface of battleship steel underlain by 24 feet of concrete, and attempted to puncture it at various angles of address.
Staff members from the Western Governors’ Association and the NRC, along with DOE officials, were on hand at Sandia’s Aerial Cable Site to view the tests.
The series of tests at the remote site are designed to attack all the weak points in the package, explains Doug Ammerman (6765), project manager for the testing. But the container is designed to take the beating. “It’s really a box inside a box inside a box inside a box,” says Doug. Energy absorbers between an outer and inner box will be crushed during the tests as they do their job, and although the package will look damaged, the inner containment boundary is expected to remain leak-tight. This will be confirmed when the test unit is returned to the fabricator, Engineered Products Division, in Carlsbad. Sandians Dave Bronowski (6315), Tom Gallegos, and Terry MacDonald (both 6765) used vacuum testing during the test series to spot-check the performance on an ongoing basis.
Phil Noss, licensing manager and project engineer for the Tacoma, Wash.-based container designer, views the testing as a critical step in a four-year process. The design is based on a French container, called a TN Gemini, with a rigid inner container and an integral overpack structure (see diagram below). “Layers of foam in varying thicknesses and puncture plates with an energy absorbing structure protect the package contents,” he says.
Waste won’t go directly into TRUPACT-III, but into a “standard large box” that fits in the inner TRUPACT-III container, Noss explains. The company successfully tested a half-scale version of the container three years ago at Sandia. The process had to be repeated at full scale, however, because the NRC did not accept half-scale leak test results as representative of the full-scale package. The current full-scale package is about two-thirds as long as the original Gemini package, allowing it to meet US highway transportation weight limits, Noss says.
He and his colleagues incorporated these changes and other refinements in the current version. It was fabricated beginning earlier this year in Carlsbad, under a strict quality assurance regimen. Preliminary load testing and leak testing to establish a baseline also occurred in Carlsbad before the container was shipped to Albuquerque for testing.
Marc Italiano, project manager for DOE at Carlsbad, says the containers will be used to move 5- by 5- by 8-foot boxes, containing items such as cut-up glove boxes and other odd-shaped materials from the weapons complex that will not fit into 55-gallon drums. “This will be waste from the old weapons program . . . byproducts from production, maintenance, and disposal,” says Italiano. “Most of it fits in 55-gallon drums and that’s what we use, but there is also a lot of big stuff that won’t fit.” Many items in 4- by 4- by 7-foot boxes and quite a few in 5- by 5- by 8-foot boxes remain at DOE‘s Idaho, Savannah River, Hanford, and Los Alamos sites.
“By using TRUPACT-III, we don’t have to size-reduce the stuff, which is a very complicated engineering feat,” Italiano says. Size reduction work is expensive and can involve using robots or workers dressed in protective gear. With NRC approval, TRUPACT-III can begin to move wastes to WIPP, he says.
Before gaining NRC approval however, Noss and others at Packaging Technology will write a Safety Analysis Report. The testing process, quality assurance information, and test data will be part of the SAR. Fire testing data is being provided by computer modeling and simulations rather than in a physical fire test, Doug says. NRC officials will then review the report before making a decision on the certification of the container.
“We had a big decision about where to test initially,” says Noss. “We had considered testing at Oak Ridge and also in France. But because of the size and the complexity of the container, Sandia became the choice.”