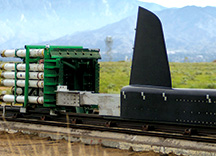
In the not-so-distant future, business travelers will be able to take off from Paris at 8 a.m. for a breakfast meeting in Manhattan or fly from New York to Tokyo in less than 10 hours.
That’s the vision of supersonic business jet (SSBJ) designer Aerion Corporation. To help make this vision become reality, Aerion turned to Sandia for assistance, hiring the Labs to conduct a Mach 1.6 test at the rocket sled track.
Jason Matisheck, Aerion business manager and manager for the Sandia tests, said Aerion performed an aerodynamic experiment that, to his knowledge, has never been attempted with a rocket sled.
“The rocket sled had several advantages when compared to other means of aerodynamic testing, such as wind tunnels and flight experiments,” Matisheck says. “Prior to the test we were concerned that the laminar flow would be adversely affected by the sled vibration, rapid change in speed, and short duration of the test.”
Despite the concerns, Aerion engineers were convinced the rocket sled represented a unique opportunity to validate at full-scale aerodynamic conditions the performance of the company’s patented supersonic natural laminar flow technology that substantially reduces drag at supersonic as well as high-subsonic cruise speeds.
“Aerion and Sandia engineers worked through several design challenges to create a viable test article for the experiment,” he says. “The test gave us the chance to record several types of data.”
Sandia tested the natural laminar flow design at Reynolds numbers approximating those on a full-scale wing at supersonic cruise conditions. The Reynolds number is the dimensionless ratio of inertial forces to viscous forces in flowing fluids and is used here to relate aerodynamic forces on wings of different scales.
The test was designed to measure data that would allow validation of the drag-reducing natural laminar flow design that is key to the SSBJ’s ability to cruise efficiently at subsonic as well as supersonic speed. Two proof-of-concept test shots were performed to prepare for the large-scale test. All three shots provided valuable information to the program.
Neil Davie (1535), lead Sandia test engineer, says the Sandia and Aerion team had to respond quickly to design and fabricate the rocket sled and test apparatus in order to meet Aerion’s schedule.
“The test approach was unique and could be described as a wind tunnel experiment in reverse, where the test item is propelled through the air instead of the other way around,” Neil says.
Sandia also implemented unique measurement capabilities with high-resolution infrared (IR) imaging through the Laser Tracker, which provided laser-guided imaging of the test wing as it accelerated from rest through Mach 1.6, Neil says. The IR imaging allowed visualization of the different aerodynamic heating rates of the laminar and turbulent boundary layers. The team recorded measurements on the test wing using an on-board digital recorder developed by Sandia.
Boundary-layer total pressure probes mounted at the trailing edge of the wing measured the thickness of the boundary layer, and accelerometers on the non-imaged side of the wing helped characterize the vibration of the wing.
The wing model used for the test was one-sixth the size of the actual wing. A cluster of five-inch-diameter rocket motors accelerated the wing at 30 gs to a speed of Mach 1.6 and maintained that speed for 1.7 seconds before hitting a water brake at the far end of the 10,000-foot-long track.
“We are still analyzing the results of the large-scale test and discussing options for a follow-on test series with Sandia,” Matisheck says.