Automated arm hefts hot pits so people don’t have to
The noblest promise of robots has been to keep people out of harm’s way — to perform tasks that are too dangerous, too difficult, or too monotonous for humans to do safely every time.On Jan. 23 at the Mason & Hanger Pantex plant near Amarillo, a Sandia-developed robotic system performed such a task — it grabbed and moved a W80 pit across a room. It was the first time a nuclear weapons pit had ever been lifted by a robot.The historic operation was the first in a final series of qualification trials for a new automated Weigh and Leak-Check System (WALS) developed jointly by engineers at Pantex and Sandia’s Intelligent Systems and Robotics Center 15200.
Safety, reliability, flexibility
Periodically war reserve pits from a variety of dismantled US nuclear weapons are pulled from storage inside Pantex bunkers, unpacked from their containers, removed from their shipping fixtures, weighed, leak-checked, repacked, and returned to storage. This month, following a final DOE review, Pantex plans to begin weigh and leak-check operations using the automated system — all but eliminating the human exposures to radiation that are routine under the current manual procedures.“WALS was developed to automate some of the highest-dose operations at Pantex, such as human handling of pits during maintenance and inspection procedures,” says project leader Bill Drotning of Applied Systems Dept. 15271.
Sandia designed, developed, integrated, and tested the WALS robotic system (a commercial robotic arm on a 25-ft. track), its control software,user interface, custom tooling (grippers and special tools the robot uses to handle the pits and fixtures), automated work cell stations, and a suite of sensors and safety features necessary to operate the robot safely and reliably. Pantex designed, developed, and tested the automated weigh and leak-check measurement stations in the WALS work cell, to and from which the Sandia robot will shuttle the pits.
To accommodate a range of different pit, container, and fixture types and sizes from a variety of US nuclear weapons, the robot incorporates computer vision to determine the positions of objects, force control to precisely and gently place pits in the work stations, and ample safety features. “We designed in several layers of safety to make sure the system could never drop or dam-age a pit,” he says. Mechanical locks and sensors ensure that a sequence of events has taken place before a pit can be let go, for instance, even after a software error or intentional act.To meet the stringent safety requirements for pit handling, the system passed more than a dozen formal reviews, says Bill. Because the operation had never been done before, new requirements were developed, as well.
Handling pits without doses
When fully operational the WALS is expected to handle 200-300 pits per year. Moving that many pits around manually would result in total doses to human workers of 2,000to 15,000 millirems per year, depending on the operations performed. Except for a few container-unpacking procedures early in the weigh and leak-check process, all direct worker contact with the pits will be eliminated by WALS. Testing and certifying the automated weigh and leak-check process for a variety of pit and shipping-container configurations ensures that safety procedures are followed to the letter every time, says Bill. Automation also minimizes manual lifting of heavy containers, fixtures, and pits.“This system is safer and more reliable than a manual process,” says Bill.
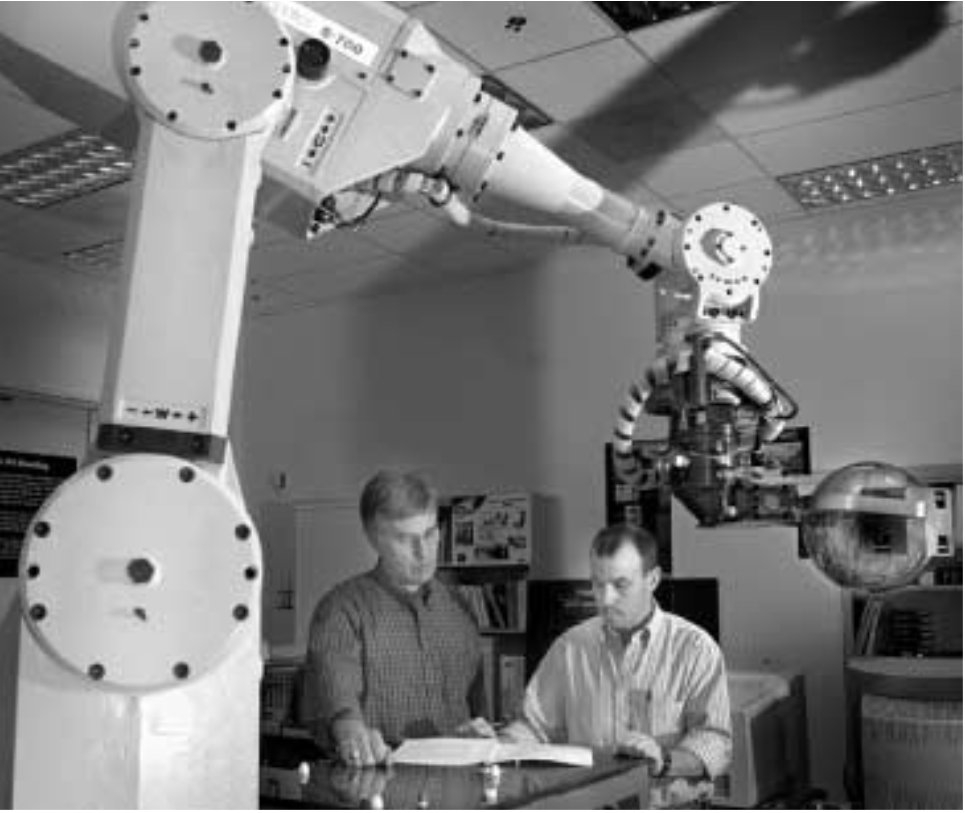
“The designs used in WALS have paved the way for future nuclear weapons-handling operations that will someday be automated.”Sandia now is working on modifying the robot’s pit-handling tools so the system can accommodate new sealed insert containers that will replace the old-style containers. Several Labs’ automated systems are already in use around the weapons complex,including a system for inventory and retrieval of pits in storage racks inside Pantex bunkers, a system for automated disassembly of gas generators at Pantex, and an automated canning system for retired plutonium, now part of a prototype plutonium-packaging line at Los Alamos National Laboratory (Lab News, May 5, 2000). The Sandia WALS team has included Bill, Al Jones (ret.), Howard Kimberly (software lead,15272), Walt Wapman (hardware lead, 15271), Brian Kast (15271), Charleene Lennox (15272),Paul Johnson (15271), Jim Majors (15271), Dave Darras (former contractor), Dan Homan (former contractor), Bob Watson (9811), Joel Kuhlmann (former employee), Carla Montoya (former employee), Kevin Jones (15272), John Webb (ret.),Ellis Dawson (1639), and Jim Spalding (ret.)