Sensor to become ‘canary in a mine’ for lab on a chip
Acoustic wave chemical sensors, each no bigger than a shirt button, promise to play an important role in Sandia’s initiatives to develop integrated microsensor systems that can detect minute traces of dangerous chemicals.
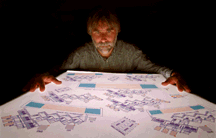
Download 150dpi JPEG image, ‘table_pix.jpg’, 1.5 Mb
In some applications, these microsensors would be similar to a “canary in a mine.” Like the canary, the sensors will be able to detect the presence of chemicals in the environment. But unlike the bird, they won’t sicken or die when exposed to the chemicals. They will simply alert people to the potential hazard.
“What’s important here is that the chemical sensing transducer and microelectronics are integrated onto a single substrate,” says Steve Casalnuovo (1715), who for the past three years has led a team of engineers and scientists from Microsystems Science, Technology, and Components Center 1700 and Physical and Chemical Sciences Center 1100 in the effort to develop the integrated sensor.
“Monolithic integration has a lot of advantages but the principal one for us is the small size of the resulting devices.”
They can be so small that an array of as many as four or five miniature sensors, each about two millimeters by 0.5 millimeters by 0.5 millimeters and sensitive to different chemicals, could be built on a chip the size of a shirt button. And because they will be tiny, the sensing system could eventually be carried by robotic vehicles to the site of a chemical spill or be worn by soldiers on a battlefield. Over the next two years, these sensors will be incorporated into a miniature chemical analysis unit by Sandia, a hand-held chemical detection system the size of a palm-top computer (Lab News, April 24, 1998).
For the base material of the sensor the researchers chose gallium arsenide (GaAs) substrates instead of the usual quartz. GaAs, which is used for special purpose microelectronics, optoelectronics, and now for integrated sensors, is the key to integrating the sensors and the electronics.
Traditionally, says Greg Frye-Mason (1715), who performs the chemical testing, acoustic wave chemical sensors are made from quartz. However, quartz can’t be integrated with microelectronics.
“Early on, we showed that GaAs made as sensitive a chemical detector as quartz and we knew that this approach had potential,” he says.
Like quartz, GaAs is piezoelectric, which is necessary to produce the surface acoustic waves for chemical sensing. At the same time, it is the best available semiconductor for fabricating the high frequency microelectronics needed to operate the sensors.
Piezoelectric materials can convert electric signals to surface acoustic waves that travel much like waves on the ocean’s surface. To make a sensor, a thin selectively absorbing polymer layer is coated on the piezoelectric surface. When specific chemicals absorb into this layer, the acoustic waves travel more slowly. This change can be detected by the sensor microelectronics, designed by Vince Hietala (1716), once the acoustic wave is converted back to an electric signal.
Sandia researchers foresee that someday the sensor electronics could possibly be connected to an alarm that would activate once the slowdown in the acoustic movement on the polymer layer is detected — serving as a warning that a certain chemical is in the vicinity.
Steve says a major milestone for the project was fabricating the acoustic sensors alongside the microelectronics without degrading the performance of either. Often when two different technologies are combined, hidden incompatibilities in the fabrication are uncovered. But in the case of these acoustic sensors, the team worked around the problem by using conventional microelectronics fabrication techniques.
Another important aspect of the research is developing new approaches to packaging the integrated sensors. The packages had to permit gases to flow over the sensor and still provide the electrical connections. Ed Heller (1713) developed a method of machining small gas flow channels into a lid that was attached directly to the GaAs substrate. A conventional integrated circuit package was then used for electrical connections. Future versions will have a microfabricated lid to reduce the volume of gas sampled.
Steve says the team is also investigating new types of acoustic wave devices that will provide more sensitive chemical detection in the future.
“We have adapted techniques developed for silicon micromachining at Sandia’s Microelectronics Development Laboratory to produce acoustic waves in extremely thin membranes of GaAs,” Steve says. “These work much like the surface acoustic wave sensors we now have but are potentially 100 times more sensitive to chemicals.”